Case Study of Mining Vehicle Optimization with Fleet Management System
Posted on October 29, 2024 by Nur Wachda Mihmidati
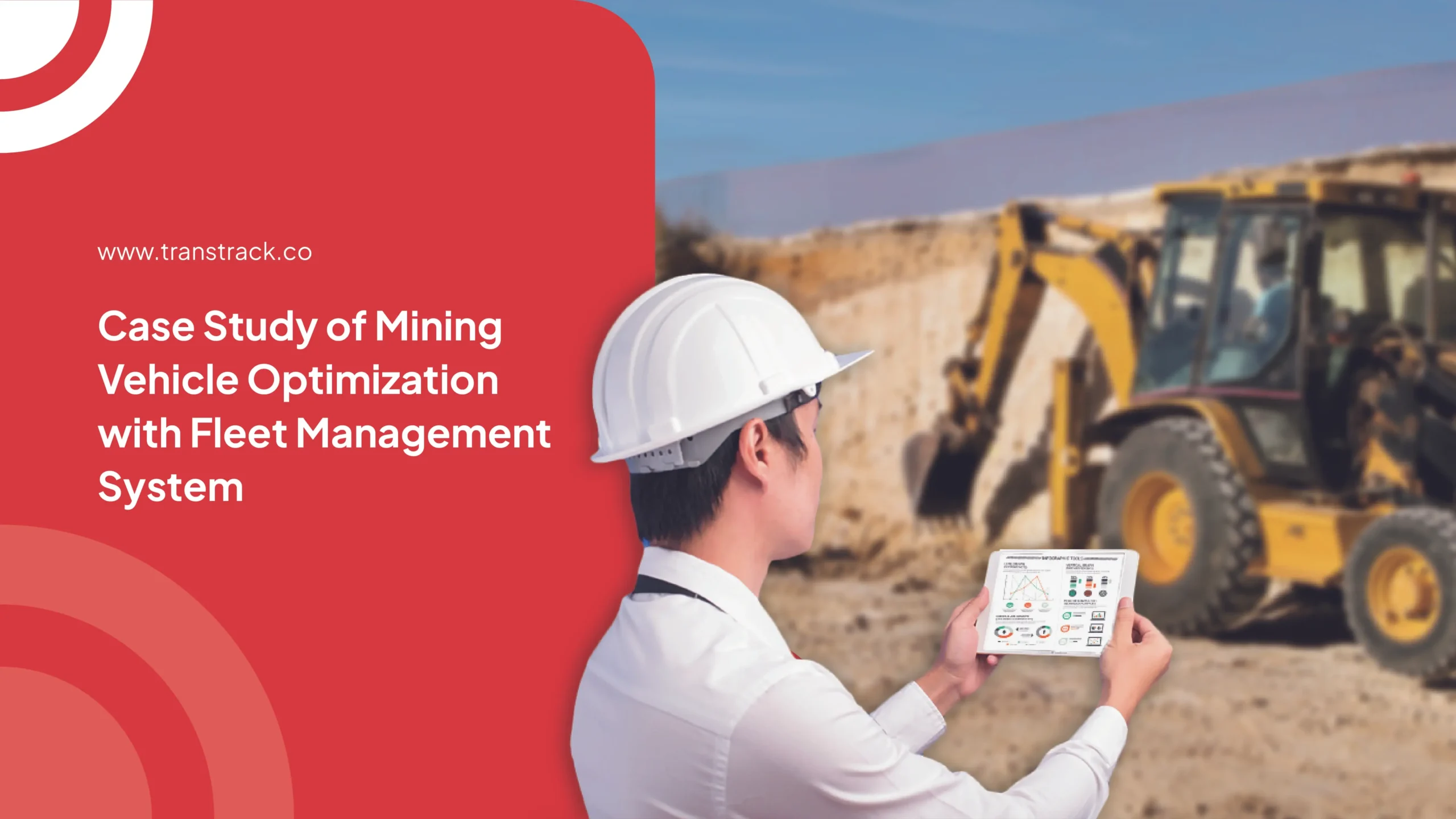
Mining vehicle management is one of the biggest challenges in the mining industry. Fleet optimization, equipment maintenance and effective communication are key to operational success. In numerous case studies, the use of fleet management systems has been proven to increase efficiency and reduce unnecessary downtime, directly impacting mine productivity and profitability. This article TransTRACK will discuss a number of solutions implemented by various mining companies to address their mining vehicle operational challenges with an advanced technological approach.
Vehicle Fuel Savings at an Indonesian Coal Mining
A coal mine in Indonesia managed to reduce fuel consumption of haul trucks by 18% thanks to the Maintenance Management solution. Before the implementation of the solution, the trucks’ average fuel consumption was 373 liters per hour. After close monitoring and corrective actions on fuel injectors and oil filters, fuel consumption was reduced to 305 liters per hour, resulting in savings of approximately US$160,000 per truck per year.
By utilizing a real-time monitoring system, Modular Mining’s Performance Assurance (PA) team identified the main causes of fuel wastage, such as incorrect injector pressure and oil filter blockage. Thanks to monitoring and proactive measures, the mine was able to improve truck efficiency, reduce the incidence of oil filter blockages that impair engine performance, and extend the life of the mining truck engine.
As a result, truck fuel consumption was significantly reduced from 373 liters per hour to 305 liters per hour, resulting in savings of nearly US$3.4 million per year for the 21 affected trucks. In addition, the mine reduced the incidence of oil filter blockages from 255,000 per week to 0. This solution demonstrates the importance of integrated monitoring and maintenance of mine vehicles to reduce operating costs and improve efficiency in the mining industry.
Vehicle Optimization at Grib Diamond Mining, Russia: Up to 80% Idle Time Reduction
The Grib diamond mine in Arkhangelsk, Russia, faced the problem of haul trucks queuing up at inoperative crushers, leading to high idle times and inefficient fuel consumption. This problem occurred due to a lack of communication between crusher operators and the central manager, resulting in trucks often being directed to the crusher even when it was down. By installing a Fleet Management System (FMS), the mine successfully addressed this issue by improving communication and automating truck assignments.
This solution resulted in a significant reduction in truck idle time, from 210 hours per month to just 38 hours per month-a reduction of more than 80% in an eight-month period. The DISPATCH FMS system not only prevents unnecessary truck queues at the crusher, but also optimizes fleet utilization by redirecting trucks to other more efficient activities such as waste hauling or parking. This improves the overall efficiency of mine operations, reduces idle time, and maximizes the utilization of the mine truck fleet.
Improved MTBF and Reduced Unplanned Maintenance at a Peruvian Open Pit Mine
A large open pit mine in Peru successfully increased the Mean Time Between Failure (MTBF) of its haulage truck fleet by more than 53% and reduced unplanned maintenance by 21% through the implementation of a Maintenance Management system and RemoteCare service. The system enables real-time monitoring of components, detecting problems before they become major breakdowns. For example, when the RemoteCare team detected a drop in coolant pressure on one of the trucks, they took immediate action to prevent engine failure that could have caused major damage.
With remote monitoring and a customized alarm system, the mine managed to prevent serious damage to the truck’s engine. One intervention avoided $250,000 worth of engine replacement costs, which when accumulated over a year can save more than $3 million. The technology not only improved maintenance efficiency but also significantly reduced unplanned downtime.
TransTRACK Solutions for Mining Vehicle Optimization
TransTRACK provides advanced solutions for mine vehicle optimization, designed to improve the efficiency, safety, and productivity of mining operations.
Fleet Management System (FMS)
- Monitor the fleet in real-time, providing full visibility into the location, status and performance of mining vehicles.
- Optimize mine vehicle travel routes to reduce fuel consumption and improve operational efficiency.
- Provide historical data and fleet performance reports for better decision-making.
Driver Monitoring System (DMS)
- Monitors driver behavior, such as sudden braking, excessive speed, and other risky driving patterns.
- Provide real-time alerts to drivers and mine operators to reduce accidents.
- Generate driver behavior reports that can be used for safety training and improvement.
Predictive Maintenance
- Utilizing sensors and telemetry data to monitor vehicle condition and predict potential component failure.
- Reduce downtime by performing maintenance before a major failure occurs, keeping mining vehicles operational.
- Reduce unplanned maintenance costs and increase the Mean Time Between Failures (MTBF).
Fuel Monitoring
- Monitors real-time fuel consumption of mining vehicles, providing visibility into fuel wastage.
- Helps identify inefficient consumption patterns and offers solutions to improve fuel efficiency.
- Generates reports that help in planning refueling and reducing operational costs.
Route Optimization
- Uses advanced algorithms to calculate the fastest and safest route in the mine area, reducing travel time and fuel consumption.
- Minimizes vehicle idling time caused by queues or inefficient routes.
- Increase operational productivity by ensuring mining vehicles are always moving on the optimal path.
Asset Health Monitoring
- Provides continuous monitoring of engine and component health, enabling proactive maintenance to extend vehicle life.
- Detect potential issues such as overheating, oil leaks, or component wear before they have a major impact.
- Reduce the risk of major failures that can lead to long downtime and high costs.
With the implementation of TransTRACK solutions, mines can achieve significant fuel savings, increase vehicle life, and reduce overall operational costs.
Optimize your mining fleet with TransTRACK’s Fleet Management solution. With features like Fuel Monitoring and Predictive Maintenance, you can reduce operating costs by millions of dollars and keep your fleet running non-stop. Contact us for industry-leading solutions that ensure maximum productivity and driver safety every step of the way!
Recent Post
Topic :