The Importance of Predictive Maintenance to Reduce Downtime in the Manufacturing Sector
Posted on September 17, 2024 by Nur Wachda Mihmidati
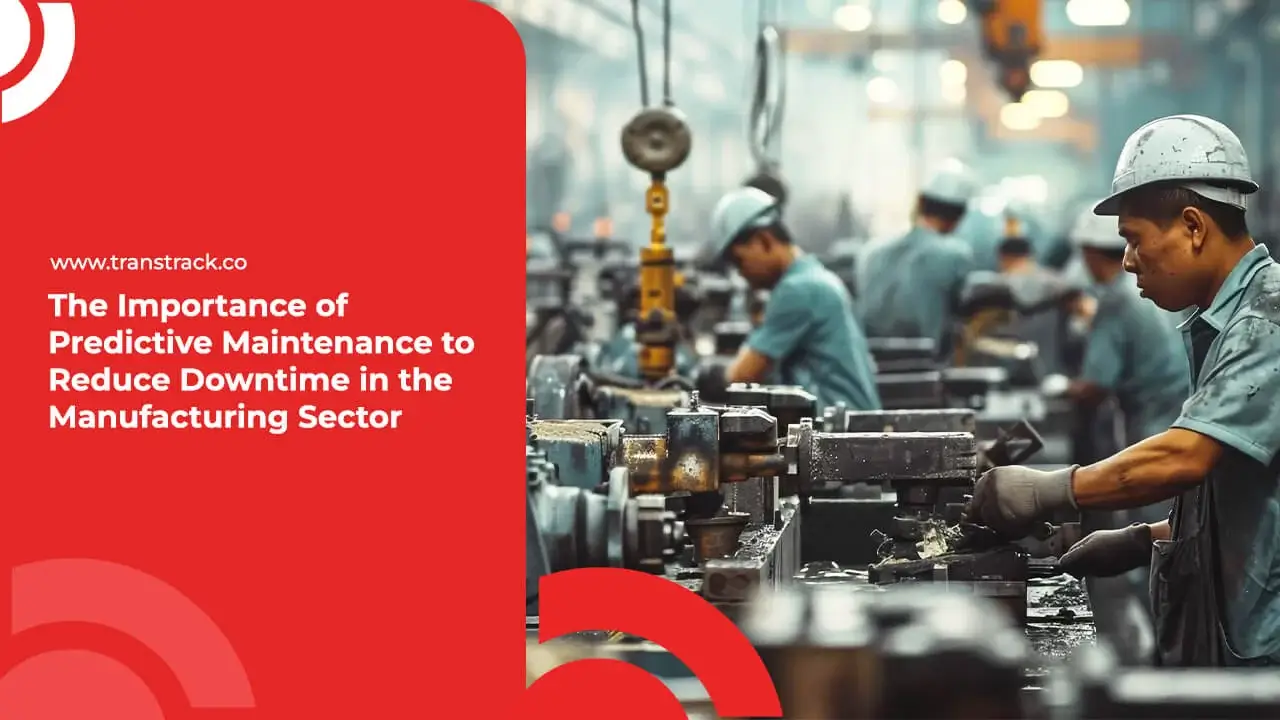
Downtime, or the time during which a machine or system is not operating, is one of the biggest challenges in modern industry that can affect efficiency and productivity. With the increasing complexity of technology and machinery, as well as higher market demands, downtime can cause significant losses in operational costs and customer satisfaction. In a competitive business environment, the ability to effectively manage and reduce downtime is key to maintaining smooth operations and achieving competitive advantage.
Identifying the causes of downtime and implementing appropriate strategies is critical to minimizing its impact. By utilizing the latest technologies, such as predictive maintenance systems based on big data, companies can monitor machine conditions in real-time and prevent breakdowns before they occur. This approach not only helps reduce downtime but also increases machine life and operational efficiency, thus providing significant long-term benefits to the company.
Downtime in the Manufacturing Sector
In the manufacturing world, relying on hope and intuition to manage machine breakdowns is no longer sufficient. With increasing machine complexity and pressure to improve uptime and productivity, big data-driven predictive maintenance is now an effective solution. Predictive maintenance collects and analyzes historical data, both structured and unstructured, to predict potential machine breakdowns before they occur. Using advanced analytics, companies can monitor critical parameters and make the necessary interventions to avoid breakdowns, thereby reducing machine downtime by 50 percent and extending machine life by 40 percent.
An example of the application of this technology can be seen in the oil and gas industry. An oil company faced significant losses due to a compressor failure on their offshore production platform, which halted production and cost them up to $2 million per day. By analyzing data from hundreds of sensors and finding patterns in parameters such as temperature and pressure, the company was able to predict the failure weeks in advance. While they couldn’t completely prevent the breakdown, they managed to reduce downtime from 14 days to six days by preparing equipment and repair personnel on site, saving millions of dollars per incident.
Case Study of DHL’s Strategy
In the Middle East, one of the oil industry’s leaders faced the enormous challenge of meeting growing demand while managing increasingly complex and dispersed operations. With operations having to function consistently across dozens of remote locations and harsh terrain, as well as the need for efficient delivery of maintenance parts, supply chain management was crucial. Previously, the company faced problems with a fragmented supply chain, lack of predictability and visibility, and complex and time-consuming processes in managing thousands of suppliers and delivery points. This decentralized approach resulted in difficulties in ensuring availability of critical materials and diverted staff focus from the core business.
DHL Supply Chain offered a solution that redesigned the distribution network and implemented an integrated system supported by a central control center. The solution included a more efficient transportation network, a material tracking system integrated with customer ordering systems, and strategic distribution points to reduce costs and environmental impact. As a result, the company was able to improve HSSE compliance, supply visibility and supplier service levels. With improved MRO supply availability and success in the Saudization program, the company not only reduced costs and increased production, but also supported continued growth with local Saudization rates reaching over 86%.
Overcoming Downtime with TransTRACK Solutions
TransTRACK offers comprehensive solutions to minimize downtime and improve operational efficiency through advanced technology and integrated systems. Here are some of the key features of our solutions:
- Predictive Maintenance System: Using historical data and advanced analytics, the TransTRACK predictive maintenance system monitors engine and vehicle conditions in real-time. This enables early detection of potential problems before they develop into serious breakdowns, so you can perform maintenance or repairs before downtime occurs. This approach can reduce downtime by up to 30% and extend engine and vehicle life.
- Real-Time Tracking: TransTRACK’s real-time tracking technology allows you to monitor the location and condition of your vehicles and equipment at any time. With this system, you can ensure that all operational assets are in the best possible condition and identify and address issues quickly. It also helps in maintenance planning and scheduling, as well as reducing downtime due to delays or logistics issues.
- Integrated Supply Chain Management: TransTRACK’s integrated supply chain management solution ensures that critical parts and supplies are available on time and in the right place. This includes inventory monitoring systems, supplier management, and effective distribution strategies, which help reduce delays and operational disruptions that can lead to downtime.
- Fleet Management Solution: TransTRACK also provides fleet management solutions that help you efficiently manage and optimize your vehicle fleet. This includes automated maintenance scheduling, vehicle performance tracking, and fleet utilization data analysis. With thorough monitoring, you can identify maintenance needs before problems occur, as well as improve fuel management and route planning to reduce downtime and operational costs.
By implementing solutions from TransTRACK, you not only reduce downtime but also improve overall productivity and efficiency. Contact us to find out more about how our technology can help you optimize your operations and achieve better results.
Recent Post
Find Out What Inbound Logistics is and How to Optimize It!
August 29, 2025Monitoring Fuel Expenditure Using Fuel Sensor
August 28, 2025Topic :
fleet managementvehicle maintenance