Discover the Work Safety Management System in Mining!
Posted on September 15, 2023 by Nur Wachda Mihmidati
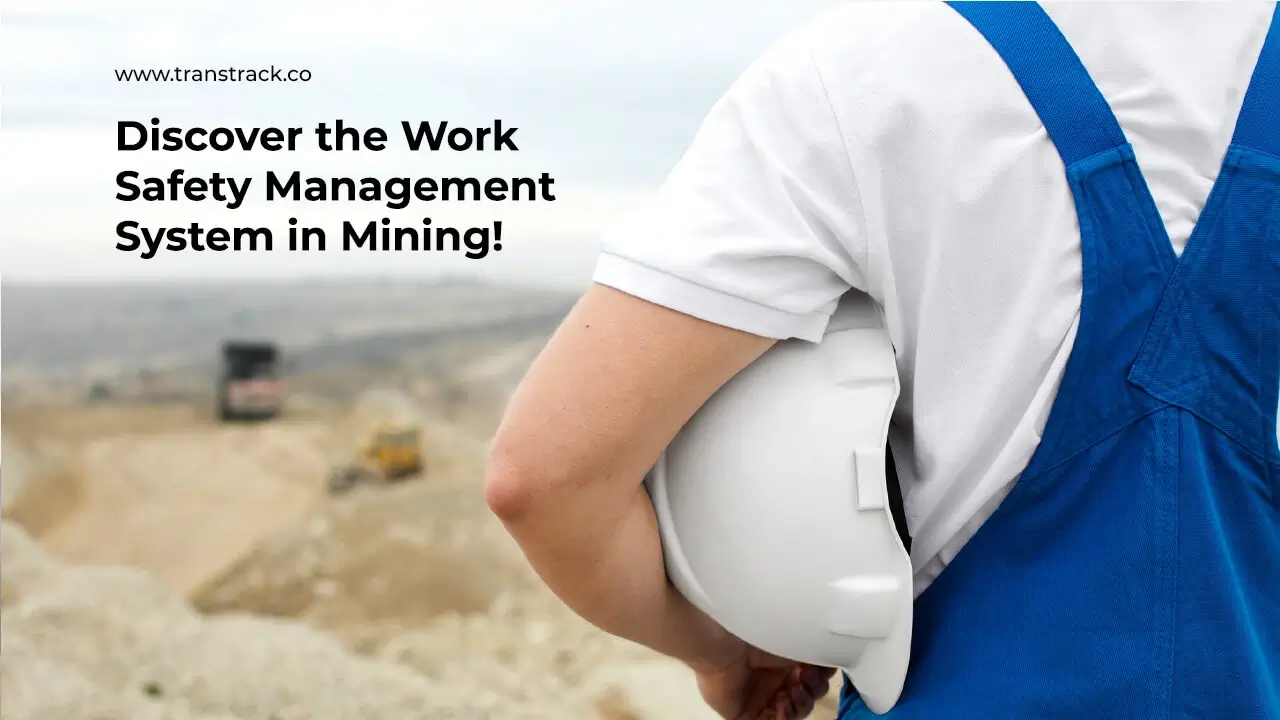
The importance of the Occupational Safety Management System (K3) in the work environment is very striking because every individual expects a work atmosphere that promotes a sense of security. This is not only true for the convenience of workers, but also for company profits.
Based on the provisions regulated by Government Regulation of the Republic of Indonesia Number 50 of 2012, the K3 Management System includes all actions aimed at guaranteeing and protecting the safety and health of workers through preventive measures against the risks of accidents and health problems that may arise as a result of work activities.
In this regulation, it is explained how the implementation of the Occupational Health and Safety Management System must be implemented. The positive impact of implementing SMK (K3) in companies is not only positive for employees, but also for the whole company. Get to know more in this TransTRACK article!
Understanding Safety Management System (SMK)
As an integral part of the overall company management structure, the OSH Management System (SMK3) involves elements such as organizational sequences, planning, implementation, procedures, responsibilities, processes and required resources.
All of this aims to develop, implement, achieve, evaluate, and maintain policies related to OSH. This approach is directed at managing risks associated with work activities, thereby creating a safe, efficient and productive work environment.
What are the Benefits of SMK in the Mining Industry?
It is hoped that the implementation of K3 in the mining sector can support the achievement of the zero accident goal which is the government’s focus, especially in the mining sector. As part of the Proxsis Group, Synergy Solusi has played a role in helping companies implement K3 management systems, both in the transportation, manufacturing, oil and gas, and mining sectors.
Their role is not limited to implementing K3 alone, but also includes efforts to increase the knowledge and competence of individuals within the company through a series of training tailored to the needs of each company.
Increasing Employee Awareness of Occupational Health and Safety
The existence of regulations related to work safety has the potential to raise higher awareness among employees regarding the potential dangers and risks that exist in their work environment, so that they become more vigilant in maintaining their health.
Furthermore, the awareness possessed by staff regarding OHS aspects can also contribute to the company’s efforts to reduce the risk of work accidents and encourage the implementation of more effective preventive measures.
Improving Confidence and Corporate Image
Increased confidence and corporate image were able to occur thanks to the availability of benefits related to occupational health and safety. Information about this that spreads widely in cyberspace can attract the attention of the best prospective employees to apply for jobs at the company.
Not only that, a positive reputation also plays an important role in attracting other companies and institutions to establish close cooperation with the company. However, if facilities related to occupational health and safety do not exist, then the company can be considered to have weaknesses.
Employee Performance Improvement
The existence of protection for occupational health and safety provides a sense of security and comfort to employees, which in turn can encourage them to work with higher productivity. Over time, employee performance also tends to increase.
Building an Efficient Management System and Reducing Losses
Having an understanding of occupational health and safety allows potential accidents to be anticipated and minimized more effectively. One aspect of the K3 framework is the arrangement of working hours and overtime schedules for employees, which aims to reduce the impact of stress due to working too long. Stress can contribute to the emergence of various diseases that are detrimental to employee performance. Negative impacts such as absences due to illness or work accidents experienced by employees can be reduced by the company.
Issues regarding occupational health and safety have very high relevance in the work environment. K3 represents absolute awareness that should be given by the company to employees in order to create a comfortable work environment.
For optimal implementation of the K3 Management System, a strong understanding of the aspects of occupational safety, health and safety is a must. In an effort to increase employee work activities, it is also necessary to provide technology such as computers that suit the needs of each individual. Asani offers laptop and computer rental services with the best quality and competitive prices.
[display-post-read-also]
Elements of Safety Management Systems in Mining
There are 7 elements of SMKP, starting from policy making which is not just a formality, but also requires careful adjustment to field conditions. Planning is an important basis for managing risk management and complying with applicable regulations.
Organizational and personnel elements show the importance of the presence of individuals who have specific roles in K3 management, including emergency response teams and safety committees. Implementation and evaluation reflect the importance of proper implementation and continuous monitoring of performance and safety in the field.
All of these steps must be supported by neat documentation and in accordance with established standards. All of these elements form a solid foundation in creating a safe, efficient and quality mining environment for all workers involved.
Conclusion
A Safety Management System in Indonesian is an important component of any work environment that cares about employee welfare and business sustainability. By understanding the basic concept of SMK and the steps for its implementation, companies can create a safe and productive environment for everyone involved.
Don’t forget to always prioritize safety, because investing in safety is an investment in the company’s future.
Apart from maintaining a safety management system, your company must also pay attention to the performance of heavy mining equipment to support the work of its employees. By using the innovative TransTRACK Vehicle Maintenance System, you can find the best solution to keep your heavy equipment loader in the best condition. Equipped with various advanced features, TransTRACK provides complete control over maintenance schedules, spare parts monitoring, and real-time tool performance reporting.
Improve the performance of your heavy equipment loader through the TransTRACK Vehicle Maintenance System now. Enjoy our free practical presentation and see for yourself how TransTRACK can help you optimize machine operations, reduce downtime and increase the efficiency of your projects. Don’t let treatment hold you back. Make TransTRACK your trusted partner in managing heavy equipment.
Topic :