Lead Time Optimization in Various Sectors: A Case Study in Improving Operational Efficiency
Posted on October 2, 2024 by Nur Wachda Mihmidati
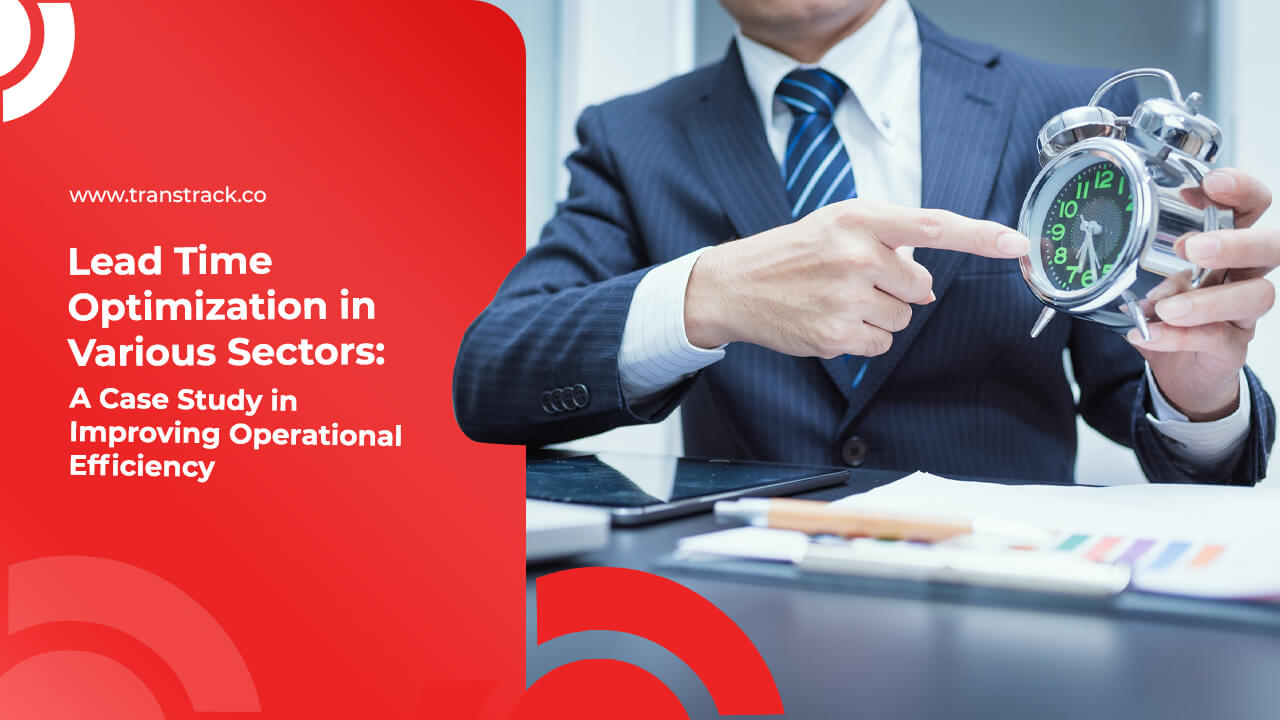
In an era of increasingly fierce global competition, companies in various sectors face significant challenges in terms of operational efficiency, especially in managing lead time. An optimized lead time is key to improving productivity and meeting customer demand in a timely manner. Various case studies show that companies that successfully optimize lead times can reduce operational costs, improve customer satisfaction, and speed up the delivery process.
This article will review several case studies from the FMCG, timber transportation, and logistics sectors, highlighting the strategic steps taken to reduce lead times. With a focus on technology implementation, efficient fleet management, and internal process improvements, we will see how these companies have managed to improve their performance and overcome challenges. Through a deep understanding of these strategies, other companies can find inspiration and solutions to achieve better operational efficiency.
Lead Time Optimization in the FMCG Industry
A processing company that uses COPRA to extract vegetable oil successfully optimized lead time in inbound logistics with the main focus of reducing Truck Turn Around Time (TTAT) by 70%. Improvements were made by reorganizing facilities such as security gates, weighbridges, loading bay layout, and warehouse space management. In addition, more organized internal procedures and collaboration with truck operators helped streamline the process. By monitoring truck arrival and departure data for 30 days, the company was able to identify the obstacles causing delays and find solutions to speed up the process.
The result of this lead time optimization can be seen in the reduction of the average TTAT time from 8 hours 51 minutes to 4 hours 5 minutes, which translates to a time saving of approximately 56 minutes per truck. This time reduction allowed the company to double the number of trucks processed per day without increasing labor, while reducing the cost of delays by Rs11,52,000 per year. With shorter lead times, processing becomes more efficient and overall productivity increases, responding to the growing demand from the market.
Timber Transportation Lead Time Optimization with Fleet Management Strategy
Lead time in log transportation management is highly dependent on the availability of transportation fleets, especially when facing the risk of timber quality deterioration due to environmental factors such as insect infestation and blue stains. Traditional management strategies such as “Oldest Wood” and “Random” tend to lengthen lead times as timber harvesting is done without considering quality conditions that change over time. As a result, timber that should be transported immediately is left longer, causing a decline in quality and economic value. In the context of limited fleet capacity, lead time management is key to maintaining the efficiency of the timber supply chain and minimizing the risk of loss.
The use of quality-based strategies such as “Quality FIX” and “Quality VAR” enables more dynamic and efficient fleet management by prioritizing the transport of timber at risk of devaluation in the near future. These strategies significantly reduce lead times by optimally utilizing existing fleet resources. In addition, strategies such as “Quality MULTI” that use multimodal transportation (a combination of truck and rail) can speed up the transportation process, especially when the truck fleet is limited. By reducing lead times, the value of salvaged timber increases up to 73%, showing how important synchronization between fleet capacity and transportation needs is in maintaining timber quality.
Fleet Lead Time Optimization in Logistics Companies
In a case study in the logistics industry, their main focus was on the effect of fleet availability and control on smooth delivery, which directly affects fleet lead time. Fleet availability was categorized as good, but there were issues with the age standard of the fleet in use. Fleet rejuvenation is urgently needed to ensure that vehicles remain in optimal condition for delivery. In addition, control over the implementation of KPIs in each division shows the need for strengthening to improve delivery accuracy and efficiency. Accuracy in recording and adjusting the number of goods is also an important factor that contributes to smooth delivery, so that lead time can be minimized.
The clarity and completeness of information in shipping documents also greatly affects lead time. Incomplete information in the documents can cause delays in the delivery process. Therefore, it is important for logistics companies to ensure that all shipping documents are compiled completely and accurately. The results of the analysis show that fleet availability and control have a strong relationship with smooth delivery, with a contribution of 88% respectively. By implementing recommendations such as fleet rejuvenation, clear KPI implementation, and improved documentation, logistics companies can optimize fleet dwell time, ensuring more efficient and effective delivery of goods.
TransTRACK’s Solution to Reduce Fleet Lead Times
TransTRACK offers an innovative solution to reduce fleet lead times, which is key in improving the operational efficiency of logistics companies. Using an integrated Fleet Management System (FMS), TransTRACK enables real-time monitoring of fleet conditions. Here are some of the features of TransTRACK that can help reduce lead times on fleets:
- Real-Time Monitoring: The system enables live monitoring of fleet conditions, including vehicle location and status, so that companies can optimize delivery routes.
- Intelligent Route Management: This feature analyzes traffic conditions and recommends the best route to avoid congestion, reducing travel time.
- Proactive Maintenance Schedule: TransTRACK provides data-driven maintenance reminders and schedules to ensure fleets are always in optimal condition and reduce the risk of breakdowns.
- Performance Reporting: The system provides analysis of fleet and delivery performance, helping companies identify areas that need improvement for better efficiency.
- Delivery Document Integration: This feature ensures all shipping documents are complete and easily accessible, reducing delays caused by documentation issues.
- Notifications and Alerts: The system sends notifications to drivers and managers about conditions that affect deliveries, such as bad weather or traffic disruptions, enabling a quick response.
With the implementation of these features, TransTRACK helps logistics companies reduce lead times, improve operational efficiency, and ultimately increase customer satisfaction.
Schedule a free demo with TransTRACK today and discover how our solution can significantly reduce your fleet’s lead time. Optimize operations and increase customer satisfaction with our advanced technology!
Recent Post
Topic :