Know the Types, How to Calculate, and Purpose of Logistics Costs!
Posted on July 5, 2023 by Nur Wachda Mihmidati
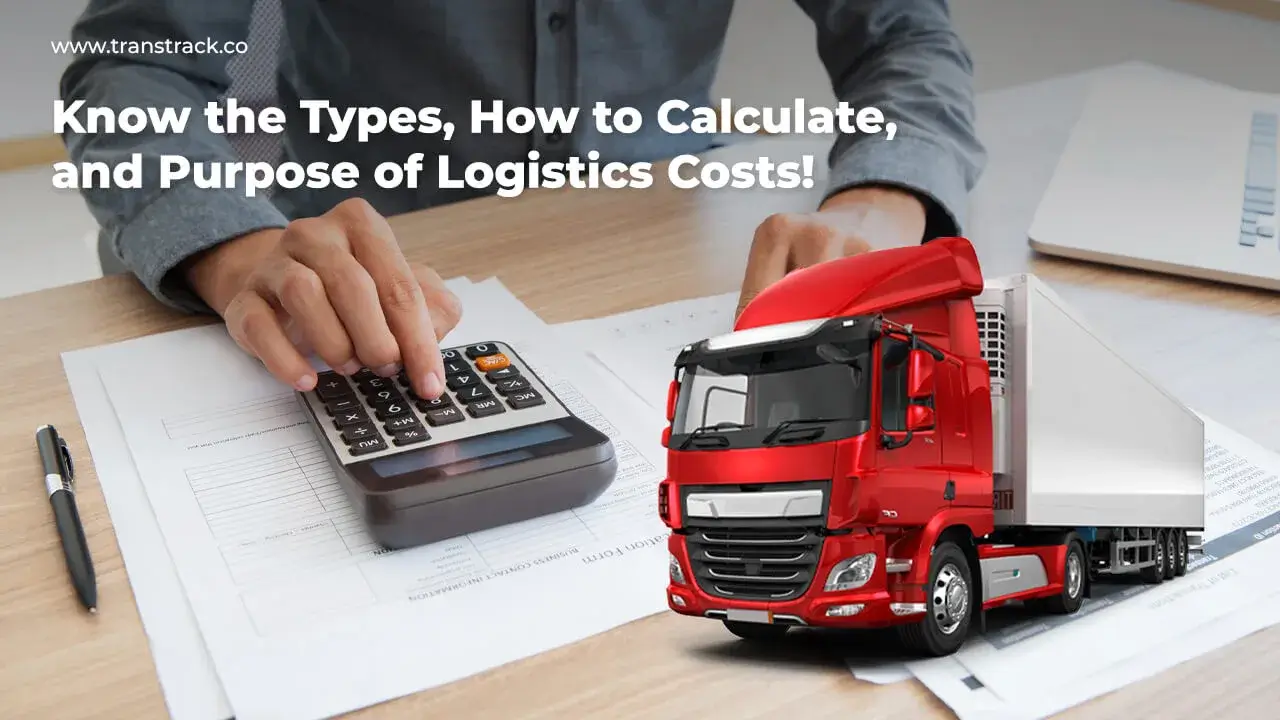
Logistics costs refer to all costs associated with planning, implementing and controlling the flow of goods and services from source to final destination. This includes costs incurred during the process of procuring, producing, storing, packaging, shipping, distributing and returning goods.
This comprehensive understanding of costs helps companies to identify areas where efficiency can be improved, manage risks, and optimize the overall flow of goods and services. Check out the following TransTRACK article for more details!
Types of logistics costs
The following is a further explanation of each of the types of fees you mentioned:
Transportation and Shipping Costs
This includes costs associated with shipping goods from one location to another, such as fuel costs, driver fees, vehicle maintenance fees, insurance fees, toll fees, road maintenance fees, vehicle rental fees and international transportation costs.
Warehouse Cost
This involves costs associated with storing and managing goods in warehouses, including warehouse rental or ownership costs, warehouse management system costs, warehouse equipment costs, warehouse labor costs, warehouse security costs, and warehouse maintenance costs.
Inventory Cost
This includes costs associated with storing, managing, and processing inventory, such as physical storage costs, inventory insurance costs, inventory obsolescence costs, loss costs, inventory scanning costs, and inventory control costs.
Distribution Fees
This involves costs associated with the process of distributing goods from factories or warehouses to customers, including order processing costs, packaging costs, shipping costs, material handling costs, distribution administrative costs, information technology costs, and distribution monitoring costs.
Labor costs
It includes costs related to the workforce involved in the logistics process, such as logistics employee salary costs, employee training costs, workforce management costs, employee benefit costs, and workforce security costs.
It is important to note that this list includes only a few common types of fees. Sometimes, there are also other costs which may be relevant depending on the industry and the complexity of a company’s supply chain.
How to calculate logistics costs
Calculating costs involves tracking and aggregating all the cost components associated with planning, implementing, and controlling the flow of goods and services from source to final destination. Here are the general steps in calculating logistics costs:
Identification of Cost Components
Identify all relevant cost components, including transportation costs, warehouse costs, inventory costs, distribution costs, labor costs, and other cost components specific to your logistics operations.
Data collection
Collect the necessary data for each cost component. This can include invoices, expense records, shipping documents, financial reports and other relevant information related to logistics activities.
Cost Categorization
Group costs into appropriate categories, such as transportation costs, warehouse costs, inventory costs, and distribution costs. This will assist in further analysis and monitoring of logistics costs.
Cost Calculation
Calculate the cost for each component using the data collected. For example, for transportation costs, add up the fuel costs, driver fees, vehicle maintenance costs, insurance costs, and other costs related to the transportation of goods.
Analysis and Evaluation
Analyze and evaluate the calculated costs. Identify areas where efficiency can be improved or costs can be reduced. This can help you identify opportunities to improve operational efficiency and optimize the flow of goods and services.
Monitoring and Reporting
Once you have calculated your costs, it is important to continue to monitor and track them regularly. Generate regular reports to monitor cost developments and identify spending trends and patterns.
It is important to note that the costing process may vary depending on the complexity of your logistics operation. You can also use a logistics management system or specialized software to help you collect data and calculate costs more efficiently.
[display-post-read-also]
The purpose of knowing the logistics costs
Knowing logistics costs has several important goals that can provide benefits to the company. The following is an in-depth explanation of these objectives:
Cost Control
The main purpose of knowing logistics costs is to control company expenses. By understanding and calculating logistics costs effectively, companies can identify areas where costs can be reduced, efficiency can be increased, and waste can be avoided. This helps to increase the company’s profits and ensures sustainable operational continuity.
Better Decision Making
Accurate and detailed information on logistics costs enables companies to make better decisions. For example, knowing the cost of transportation, a company can choose the most efficient and economical shipping option. By knowing the cost of inventory, companies can determine optimal inventory levels to avoid excessive storage costs or inventory shortages that can cause lost sales.
Performance Monitoring and Evaluation
Knowing logistics costs allows companies to monitor and evaluate their logistics performance. By comparing expected costs with actual costs, companies can identify discrepancies and take corrective action if necessary. Cost monitoring also helps in identifying cost trends over time, monitoring the effectiveness of changes made, and identifying long-term cost-saving opportunities.
Planning and Budgeting
Knowing logistics costs helps companies in effective planning and budgeting. By estimating and calculating costs accurately, companies can allocate resources appropriately for logistics operations. This information is also needed in developing a realistic budget for logistics activities, including transportation, warehouse, inventory, distribution, and labor.
Improved Efficiency and Customer Service
Knowing these costs helps companies improve operational efficiency and customer service. By understanding the significant cost components, companies can identify opportunities to optimize the flow of goods and services, reduce delivery times, reduce inventory costs, improve delivery reliability, and increase responsiveness to customer demands.
Contract Negotiations and Relations with Suppliers
Good knowledge of logistics costs allows companies to better negotiate contracts with suppliers and logistics partners. By understanding the costs involved, companies can identify key bargaining points and ensure that the resulting agreement benefits both parties. Knowledge of costs also allows companies to better evaluate the performance of their suppliers and logistics partners.
By knowing costs in depth, companies can optimize their supply chain, improve operational efficiency, reduce waste and achieve competitive advantage.
In facing the complexity and challenges in logistics cost management, companies can take advantage of innovative and effective solutions such as the Logistic Service Integrator offered by TransTRACK.
With Logistic Service Integrator, companies can monitor, track and manage all their logistics processes easily and efficiently. From inventory management, order processing, shipping, to supplier performance monitoring, all logistics information can be accessed in real-time via a single platform.
So, don’t hesitate to take advantage of innovative solutions like Logistic Service Integrator from TransTRACK to manage your logistics costs more effectively. Contact TransTRACK today for more information and start optimizing your supply chain for greater success.
Topic :