What is a Backorder? Here are the Causes and Tips to Avoid Them!
Posted on May 15, 2024 by Nur Wachda Mihmidati
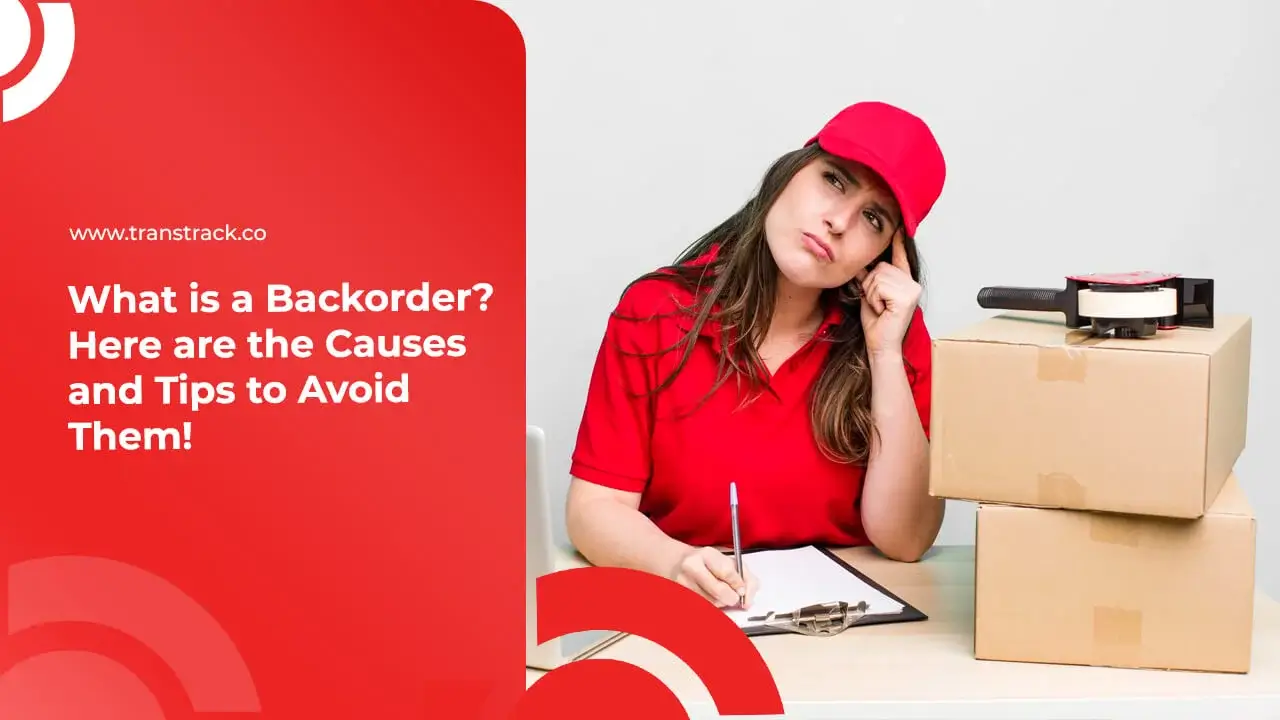
Backorder can make the supply chain process worse. An efficient supply chain is the key to any successful business. However, despite the best efforts to plan and manage inventory, companies often face challenges in the form of backorders. Backorders, a situation where customer demand exceeds stock availability, can be a source of frustration for customers and disrupt overall business performance.
In this TransTRACK article, we will explore the various causes of backorders, their impact on business, as well as strategies and solutions to avoid or reduce the likelihood of such situations occurring. With a deep understanding of these issues and the implementation of the right strategies, you can improve your supply chain performance, improve customer satisfaction, and avoid business losses due to backorders.
Let’s start with a deeper understanding of what causes backorders and how they impact your business operations.
Definition of Backorder
Backorder is a term used in inventory and sales management to refer to a situation in which a customer orders or places an order for an item that is not currently available or in stock, but will be backordered or fulfilled by the supplier at a future time. In other words, this situation occurs when a customer orders an item that is out of stock, and the company has to wait for additional inventory from the supplier before it can deliver the item to the customer. This can happen due to unexpected demand or because the company did not forecast the demand accurately. Backorder management is important to keep customers satisfied and minimize business losses due to stock shortages.
Causes of Backorders
Common causes of backorders include:
Unexpected increase in demand
When demand suddenly increases significantly, the company may not have enough inventory to meet the demand, thus causing the situation.
Lack of attention to safety stock
Safety stock is the additional stock maintained by a company as a backup to cope with fluctuations in demand or delays in supply. If companies do not pay attention to or properly manage the level of safety stock, then they are vulnerable to backorders when there is a surge in demand or delays in supply.
Warehouse management issues
Inability to manage the warehouse efficiently, including issues such as inventory errors, errors in order processing, or lack of coordination between departments, can lead to back order situations.
Problems with manufacturers or suppliers
Delays in deliveries from manufacturers or suppliers, whether due to production problems, logistics problems, or other issues, can lead to backorders because the company cannot obtain the promised inventory on time.
Tips to Avoid Backorders
The following tips can help companies avoid backorders:
Provide safety stock
Safety stock is an additional amount of stock maintained above normal levels in anticipation of demand fluctuations or supply delays. It is important to determine the appropriate level of safety stock based on an analysis of historical demand, delivery times from suppliers, and other factors that affect the availability of goods. Having adequate safety stock can help you fill stock gaps quickly in the event of a surge in demand or unexpected supply delays.
Provide real-time reports
An inventory management system integrated with real-time reporting capabilities allows you to track inventory in real time, monitor customer demand, and identify potential backorder risks quickly. With easy access to real-time information on stock items and order status, you can take proactive measures such as adjusting orders or finding alternative supplies to prevent backorders.
Reach out to more manufacturers or suppliers
Expanding your supplier network or working with multiple suppliers for the same product can help reduce the risk of supply delays as you have alternative resources. Also, establishing strong relationships with suppliers and having regular communication can help you get informed about possible delays in supply so that you can take appropriate action quickly.
Prioritize stock of fast-selling items
Sales trend analysis can help you identify the products that customers are most interested in and prioritize inventory management for those items. This could mean increasing inventory levels or distributing stock more evenly for items that are in high demand. By focusing efforts on stocking items that are most important to customers, you can reduce the risk of backorders on key items that could potentially run out of stock faster.
Ensuring a smooth and efficient supply chain is key to success for any business. However, managing backorders can be a complex challenge. With the right solution, you can reduce the risk of backorders and increase customer satisfaction.
TransTRACK offers solutions Logistic Service Integrator that can help you overcome challenges in your supply chain. By using advanced technology and an extensive supplier network, we ensure on-time delivery and high operational efficiency.
Don’t let backorders hinder your business growth. Find the right solution with TransTRACK today and improve your supply chain performance!
Recent Post
Negative Impact of Arrogant Driver Behavior on Traffic Safety
October 31, 2024TransTRACK® Presents at Australia’s Largest Roads & Traffic Expo
October 30, 2024Topic :