Preventive Maintenance, Routinely Check Your Vehicle for Safe Use!
Posted on December 6, 2023 by Nur Wachda Mihmidati
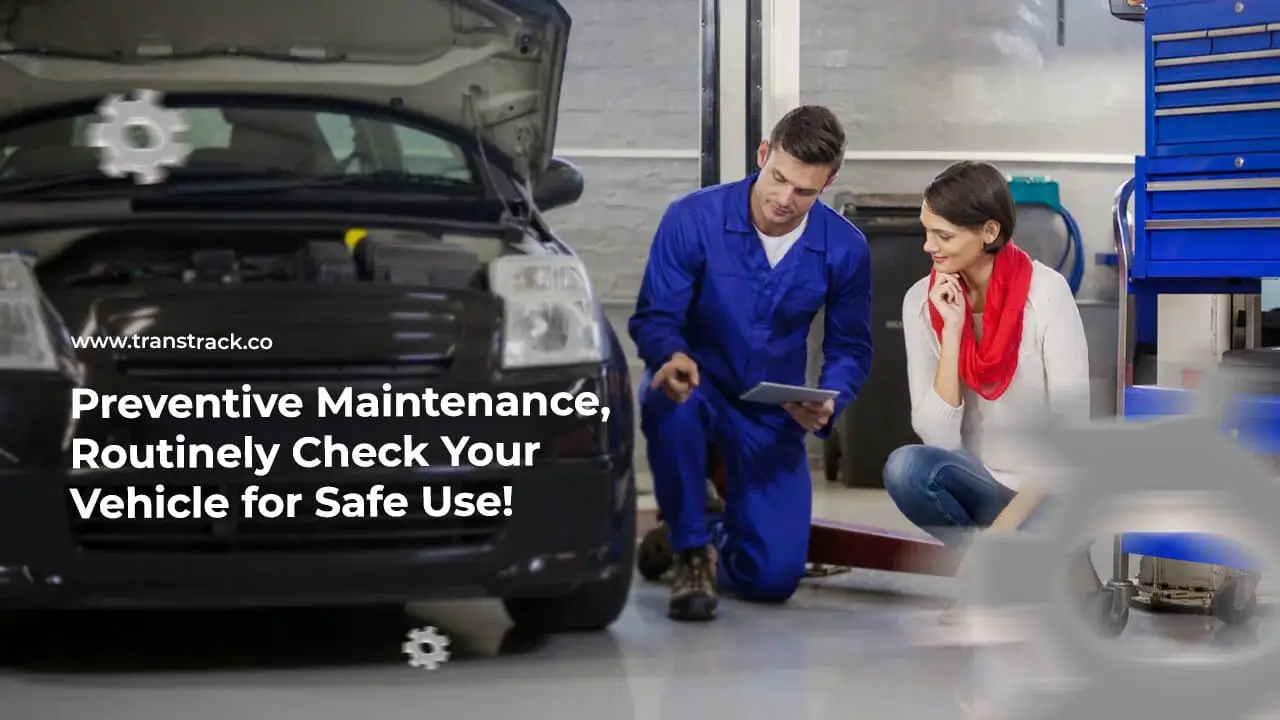
Preventive Maintenance is the regular, scheduled task checks (lubricants, chain or belt adjustments, etc) performed on assets and equipment to ensure they perform as the manufacturer intended. When executed correctly, Preventive Maintenance from TransTRACK also benefits our facility management strategy by increasing asset life, reducing downtime, and more.
Preventive Maintenance should be performed on equipment outside of its regular operating hours so as not to disrupt production or operation time. Establishing a Preventive Maintenance schedule for our key equipment ensures high efficiency and productivity in our facility.
What Types of Preventive Maintenance Are?
Preventive care is a general term. So it needs more study to be learned. Here are some of the most common types:
Time-based maintenance
Creating a monthly or annual maintenance schedule that matches the manufacturer’s recommendations for checking and cleaning the equipment will go a long way in keeping us on track. Even beyond these recommendations, we should remember that the equipment that is most critical to our business should be checked regularly to ensure the best possible operation.
Examples of calendar-based maintenance might include servicing our air conditioners a month or two out from summer, refilling salt for soft water systems, and cleaning vents to meet health standards at least twice per year.
When creating a time-based Preventive Maintenance plan, or deciding what to add to it, consider the key utilities, equipment, and technologies that our business relies on for success. These should be checked regularly to ensure that our business continues to thrive. The last thing we want to do is shut down for a few days because of a problem that could have been prevented with a little planning.
To support time-based maintenance, it’s also a good idea to keep detailed records of previous breakdowns and problems with tools and equipment, so we’ll have a better idea of which systems and equipment might need a little extra care.
Usage-based maintenance
If our business uses certain machines or equipment on a daily basis, it is a good idea to track usage (i.e. equipment monitors, operating hours, production cycles), especially if the equipment does not automatically generate tickets or notifications when a certain number of operating hours have been reached. This is referred to as usage-based maintenance.
Whether it’s a vehicle oil change, or a critical piece of machinery that has reached X number of hours, maintaining proper care and maintenance will ensure long-term use of critical equipment.
Predictive maintenance
Predictive maintenance relies on sensors to capture information about equipment (i.e. temperature sensors, or vibration sensors), and is generally specific to technologies that can trigger work orders if machines or equipment need to be inspected or upgraded. Predictive maintenance entails monitoring critical machine conditions to track performance, and to detect possible defects that could result in system crashes.
This type of Preventive Maintenance may be particularly relevant for manufacturing, food production plants, power and energy industries where the information obtained from predictive maintenance will allow maintenance managers to predict when system downtime may occur based on previous patterns, and to schedule maintenance tasks to reduce accidents on critical operational equipment.
Prescriptive maintenance
Similar to the patterns that predictive maintenance analyzes, prescriptive maintenance uses advanced analytics, machine learning, and artificial intelligence to generate predictions about maintenance, and also act on them. What does this mean? Basically, prescriptive maintenance makes recommendations to improve system operation, and also follows up on them itself to generate work orders and oversee the entire process.
As long as we manually inspect our critical equipment, and stick to the manufacturer’s recommendations and inspection procedures, we are already well on our way to effective Preventive Maintenance-no prescriptive maintenance required!
Now that we understand more about the different types of Preventive Maintenance mentioned above, we will dive into the benefits of standard Preventive Maintenance practices.
Benefits of Implementing Preventive Maintenance
Of course, one of the most obvious benefits of implementing Preventive Maintenance is that we are more likely to avoid problems before they occur. That’s the whole point, right? But if we’re still not convinced, there are some specific advantages we might want to consider:
- Preventive Maintenance will reduce downtime and business closures due to unexpected equipment failures;
- Preventive Maintenance will increase equipment life expectancy, so we will spend less money in the long run;
- Preventive Maintenance will ensure all equipment and employees work only during scheduled hours, eliminating the need to pay overtime due to unexpected machine breakdowns, etc.
- Preventive Maintenance will significantly reduce safety risks for employees and customers, thereby reducing the risk of costly lawsuits and workers’ compensation.
- Preventive Maintenance means less energy consumption for our assets and equipment due to high levels of operational efficiency, which will reduce our electricity bills.
These are just some of the specific benefits that come with regular Preventive Maintenance. Even if you own a small retail shop or food stall and don’t work with heavy machinery or equipment, Preventive Maintenance applied to your business will go a long way in reducing costly accidents and damages.
Advantages of Implementing Preventive Maintenance
There are two main advantages to using Preventive Maintenance as our primary maintenance strategy: Being able to plan maintenance tasks and not requiring condition-based monitoring.
Preventive Maintenance programs allow us to plan maintenance tasks that reduce costs and increase our productivity in the long run. Facility managers can prevent incipient failures (equipment imperfections that can lead to catastrophic degradation or failure if corrective action is not taken).
Unplanned and reactive maintenance has many overhead costs that can be avoided during the planning process. Unplanned maintenance costs include lost production, higher parts and shipping costs, and time lost responding to emergencies and diagnosing faults when equipment is out of service. Unplanned maintenance typically costs three to nine times more than planned maintenance.
When we have a maintenance plan, it is easy to reduce our program maintenance costs. Equipment can be shut down to coincide with production downtime. Prior to decommissioning, all necessary parts, supplies, and personnel can be assembled to minimize the time required for repairs. These proactive maintenance measures reduce the total cost of maintenance activities. Safety is also improved as equipment breaks down less frequently compared to less complex strategies.
In addition, Preventive Maintenance programs do not require condition-based monitoring. This eliminates the need (and cost) of conducting and interpreting condition monitoring data and following up on the results of those interpretations. It also eliminates the need to own and use condition monitoring equipment.
Difference between Preventive Maintenance and Corrective Maintenance
1. Corrective Maintenance (CM):
CM is a type of maintenance task or action that is usually performed after an equipment failure. It is simply considered as all activities that restore a failed or damaged asset to its normal working condition. It is reactive in nature. Whenever an asset fails, it is either replaced, repaired, or returned to operation.
2. Preventive Maintenance (PM):
PM is a type of maintenance task or action that is usually performed before an equipment breakdown. It is simply considered as all activities that maintain an asset and prevent it from failure or damage. It is preventive in nature.
Difference between CM and PM:
Corrective Maintenance | Preventive Maintenance |
CM is performed after asset failure or after a fault occurs. | PM is performed before asset failure or before a fault occurs. |
It is a less complicated and simple process as it does not involve any planning to prevent the asset from failure. | It is more complex compared to CM as it involves planning to prevent assets from failing. |
It can be more expensive than PM because some equipment failures cause greater system damage. | It can be expensive but prevents assets from failing. |
It can affect the system as a whole because multiple asset failures can lead to greater production losses. | It prevents loss in production by reducing the probability of failure. |
CM causes expensive repairs along with scheduled repairs. | PM mainly aims to avoid costly repairs and corrective actions. |
It is performed at random intervals because it is only performed when a failure occurs. | It is performed periodically because asset maintenance is important and should be checked regularly to avoid failures from occurring. |
CM generally increases the need for preventive action of the asset. | PM generally reduces the need for corrective actions. |
CM overall reduces asset lifecycle. | PM overall increases the asset lifecycle. |
This process results in loss of production, loss of product quality, loss of time. | This process leads to increased production, improved product quality, no loss of production time. |
This is not good for employee safety and the work environment as it increases the risk of injury. | Better for employee safety and the work environment as it reduces the risk of injury. |
More asset downtime in CM. | Asset downtime is less in PM. |
It requires more employees or technicians to perform CM. | It requires fewer employees or technicians to perform PM. |
This increases the workload for technicians. | This reduces the workload for technicians. |
Preventive maintenance is something that we must pay attention to regarding vehicle maintenance. For this reason, it is important to do regular checks. Start using Vehicle Maintenance System to extend the life of your vehicle and make sure your vehicle is always safe and ready to use. Manage vehicle, inventory, and mechanic repair and maintenance schedules and costs with TransTRACK!
Recent Post
Topic :