Heavy Equipment Maintenance, Check out the Types and Maintenance Tips!
Posted on December 19, 2024 by Nur Wachda Mihmidati
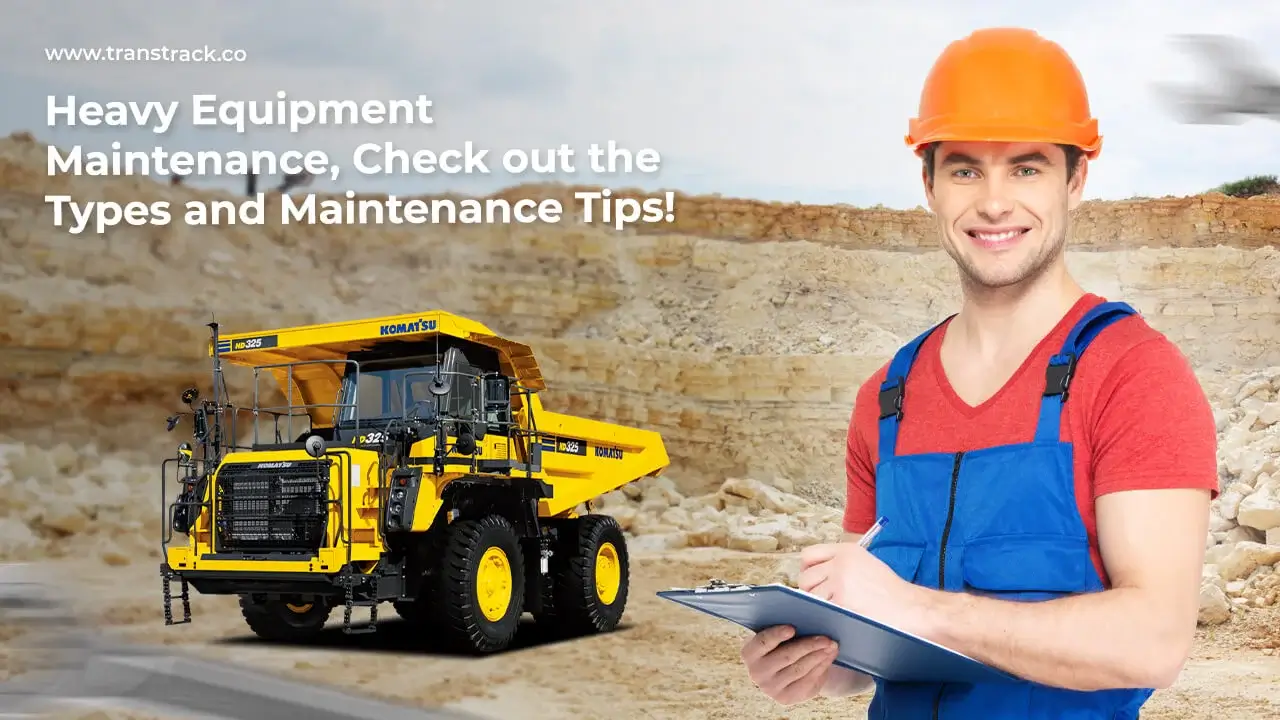
Heavy equipment maintenance is the process of regularly inspecting, cleaning, and repairing various parts of heavy machinery, including hydraulics, engines, and moving parts.
Machine maintenance is either preventive or reactive. Preventive maintenance involves regularly scheduled maintenance of the equipment and can include oil changes, tire pressure checks, and routine cleaning.
Reactive maintenance, on the other hand, occurs when a machine fails or does not operate efficiently. It may involve more downtime than Preventive Maintenance and is more expensive as technicians diagnose equipment weaknesses.
Taking the time and occasional expense to keep equipment in good condition ensures that it will function properly when needed.
Well-maintained machines also tend to last longer than those that are not. Moreover, machine maintenance provides additional benefits to businesses. Let’s find out together with TransTRACK!
How to Determine Heavy Equipment Maintenance
A proactive machine maintenance schedule relies heavily on Preventive Maintenance (PM). Often, simple service tasks such as oil changes or coolant top-ups are overlooked for long periods of time. While these items may seem minor, they can have a major negative impact on our equipment.
Creating a comprehensive PM schedule allows us to constantly monitor our assets. Scheduling machine PMs may sound daunting, but developing a schedule can be as simple as following mileage or service hour intervals. This process can be further automated through fleet management software.
When handling our own Preventive Maintenance, consider creating work orders for each task. Work orders help us plan and execute service tasks on time and automatically update inventory levels on parts used.
Streamlining work orders through fleet maintenance software allows us to communicate with maintenance teams as soon as issues arise, helping them get to work quickly. Being in smooth communication with our team helps us track repairs easily and helps get assets back in working order.
Types of Heavy Equipment Maintenance
Well, this time we will find out about what types of heavy equipment maintenance are. These types are:
- Preventive maintenance
According to Wikipedia Preventive Maintenance (PM) is “a routine for periodic inspection” with the aim of “spotting small problems and fixing them before major problems develop”. Ideally, “nothing breaks”. The main objective of Preventive Maintenance is to perform subsequent maintenance activities without damage and failure of machinery and equipment. It includes activities such as partial or complete servicing at specific periods, oil changes, lubrication, etc.
- Predictive maintenance
This maintenance activity is also carried out in advance which means solving the problem in advance. This activity is more like a preventive measure to avoid problems. The main purpose of predictive maintenance is to determine the condition of equipment & machinery so that it can be known when maintenance activities can be carried out.
This is one of the promising ways of cost savings. It also helps estimate the stage of degradation of assets, equipment, and machinery. (Both of the above are proactive maintenance activities carried out after a certain period of time such as 30 days or 45 days especially predictive maintenance).
- Corrective maintenance
Corrective maintenance restores the equipment depending on the fault. It includes various steps after the equipment fails such as diagnosis, cause of failure then ordering replacement parts & installing new parts then testing the functionality and continuing the process.
Corrective maintenance can be divided into two parts immediate corrective maintenance and deferred corrective maintenance. In the process of immediate corrective maintenance, one has to take quick action after the failure.
On the other hand, deferred corrective maintenance, in this process the maintenance activities are scheduled later, there are many reasons behind it. Such as, replacement parts may not be available, it may take a long time, or technicians are required in some other high-priority cases.
- Routine maintenance
The main objectives of routine maintenance activities are cleaning, oiling, lubricating, changing batteries & changing oil. Routine maintenance activities can be carried out on a weekly or half-monthly basis. It depends on the equipment working.
As a professional equipment maintenance practice, one should keep the emphasis on maintenance rather than repair. In simple words, to keep our equipment in good working condition, routine maintenance should be performed regularly.
- Emergency maintenance
This activity is a reactive equipment maintenance activity. The main purpose of emergency maintenance is to prevent threats to life, property and property of the company. Emergency maintenance can be implemented to keep facilities operational and safe. Emergency maintenance is widely used in chemical plants, tenant buildings, etc.
Steps for Effective Machine Maintenance
Performing regular machine maintenance is key to maintaining optimal performance, avoiding major breakdowns, and extending the life of the equipment. The following are the steps that can be followed in performing machine maintenance:
1. Routine Inspection
- Daily Checks The operator or technician checks vital components such as tire pressure, oil level, fuel condition, and dashboard indicators before the tool is used.
- Weekly or Monthly Checks include checking the cooling system, air filter, and cable connections to ensure there are no loose or damaged components.
- Visual Inspection Check the external condition of the machine to detect cracks, leaks, or deformations in important parts such as the frame, hydraulic cylinders, and joints.
2. Lubrication of Moving Parts
- Parts such as gears, hinges, and hydraulic components should be lubricated periodically to reduce friction and prevent wear.
- Choose a lubricant that conforms to the manufacturer’s specifications, both in terms of viscosity and lubricant type.
3. Hydraulic System Maintenance
- Check the Hydraulic Oil Level Make sure the hydraulic oil level is in accordance with the manufacturer’s standards, as a lack of oil can distress the system and damage components.
- Perform hydraulic oil changes on schedule or if contamination such as water or dirt is found.
- Check Hydraulic Hoses and Fittings Make sure there are no leaks or damage to the hydraulic system hoses and connections.
4. Replacement of Worn Parts
- Components such as air filters, oil filters, brake linings, and sprocket gears usually have a certain lifespan and should be replaced before they fail completely.
- Use Genuine Parts The use of genuine parts will ensure the quality and performance of the tool remains optimal.
5. Component Calibration and Adjustment
- Components such as sensors, measuring instruments, or control systems need to be calibrated periodically to keep them accurate.
- Check tire pressure, chain tension, or position of mechanical parts to maintain machine efficiency and safety.
6. Routine Cleaning
- Remove Dirt and Dust Clean the outside of the machine regularly to prevent dirt buildup that can damage components or reduce performance.
- The cooling system, air filter, and radiator need to be cleaned to prevent overheating or decreased efficiency.
7. Maintenance Documentation and Schedule
- Keep a complete record of inspections, parts replacement, and maintenance performed.
- Follow the schedule suggested by the manufacturer and adjust it to the machine’s operational conditions.
8. Engage Monitoring Technology
- Use Sensors or IoT These technologies can provide early warnings in case of potential damage, such as changes in temperature, vibration, or pressure.
- Utilize TransTRACK for Efficient Monitoring
TransTRACK is a digital solution designed to monitor overall machine performance and operations. With TransTRACK, you can:- Manage Maintenance Schedules: TransTRACK allows you to automatically create and monitor machine maintenance schedules, reducing the risk of missing routine maintenance.
- Real-Time Monitoring: The real-time monitoring feature provides important data such as location, fuel consumption, and engine condition.
- Performance Analytics: TransTRACK provides reports and analytics that help in making data-driven decisions, thereby improving operational efficiency.
- Early Warning: This system notifies you if there are indicators of malfunction, such as overheating, low oil pressure, or components that require replacement.
9. Operator and Technician Training
- Train Operators to Recognize Early Problems Operators who understand early signs of damage can help prevent problems from becoming bigger.
- Ensure that technicians understand the specifications and latest technology of the machines being used.
By following these steps consistently, companies can keep machines in optimal condition, reduce the risk of downtime, and minimize major repair costs.
Six Tips for Heavy Equipment Maintenance
Just like we take care of our cars, homes and bodies, heavy equipment needs constant attention and care.
Here are six ways to organize the maintenance of heavy assets so that looking after them becomes a regular and effective part of our workday.
1. Develop a Maintenance Routine
During routine maintenance, we should check the amount of oil, verify fluid levels, and keep an eye out for small cracks or chips. Our equipment manufacturers should provide information on how often this should be done.
However, we should immediately attend to minor workplace events such as low fuel and punctured tires.
Avoiding these can cause significant damage the longer the equipment is forced to compensate for the damaged part.
2. Check Equipment for Signs of Wear and Tear
Looking for evidence of regular minor damage to our machines and fixing it promptly helps ward off major repairs, and keeps our assets operating at their best every day.
Doing so even extends the life of the asset.
Sometimes the signs that our machines need minor repairs or inspections are not visible by walking around or looking at gauges. For example, your machine may show evidence of a problem through its exhaust. If it is normally white or gray, a sudden change to black or a change in odor is a red flag.
Another early indicator of a potential repair issue is low fluid levels. While this may be normal for some machine functions, if it occurs too soon after a scheduled refill or routine maintenance, it may indicate a coolant leak or a faulty valve.
The machine is noisy, but if it makes unusual or unnatural noises, it’s time to check the moving parts.
Grinding, clanking, or hissing sounds are early indicators of failure in the machine’s main systems. Stay alert for changes in odor or vibration levels as well.
3. Manage Engine Fluids and Ensure Regular Lubrication
Effective fluid management doesn’t just include checking fuel and coolant levels. Lubrication is an important aspect of good machine health.
Checking lubricant levels should be a regular part of basic and preventive maintenance. When doing so, you should ensure that the lubricant shows no signs of leakage from nearby seals or hoses.
When changing the lubricant, it is best to use the type specified by the manufacturer. And while low levels of lubricant are harmful, more lubricant is not necessarily better. Too much lubricant invites grease buildup, clogging, and decreased performance.
4. Don’t Overwork Our Machines
When trying to stay on schedule or make up for lost time on a project, we may be tempted to push our staff and machines a little harder to keep supervisors, clients and accountants happy.
However, using machines beyond the recommended limits is not only dangerous and potentially violates safety regulations, but it can also shorten the life of our equipment or contribute to costly repair work.
An overworked machine puts a strain on its main components, but it also puts a strain on smaller items – gears, silicone rings and connection points.
Over time, weak or worn small parts of equipment can trigger larger failures.
5. Train Our Employees
Paying attention to preventive maintenance won’t mean much if our employees aren’t properly trained on how to use the machine properly, or how to recognize signs that the machine is out of alignment.
If our staff understand what constitutes safe behavior and why, they are more likely to follow the guidelines. Also, emphasizing that machines require special care will help employees treat them like their own.
Machine training should be standardized, precise, and regularly updated.
6. Document Service and Set Reminders for Future Improvements
Knowing what our machines need, and when they need it, is critical to their operation.
Installing regular schedules and reminders for future equipment services can keep track of documentation for us, help us budget for Preventive Maintenance, and allow us to better control our personal and jobsite time tables.
Asset management software is a modern and efficient way to track machine maintenance. Some systems, such as TransTRACK, allow scheduling on the go through the app, eliminating wasteful paperwork that can easily get lost on construction sites.
Documenting services through software allow employees across the company to access this information at any time. Data is much more securely stored than on a whiteboard or in a physical notebook.
You can schedule heavy equipment maintenance regularly by subscribing to TransTRACK’s Vehicle Maintenance System. Take your company’s operations to the next level, extend the life of your vehicles and ensure they are always safe and ready to use. Manage vehicle repair and maintenance schedules and costs, inventory, and mechanics with us. Get vehicle repair and maintenance, sales systems, inventory, maintenance cost prediction, and mechanics with a VMS subscription from TransTRACK!
Recent Post
Topic :