Hydraulic Brakes, What are the Components and How Do They Work?
Posted on November 20, 2023 by Nur Wachda Mihmidati
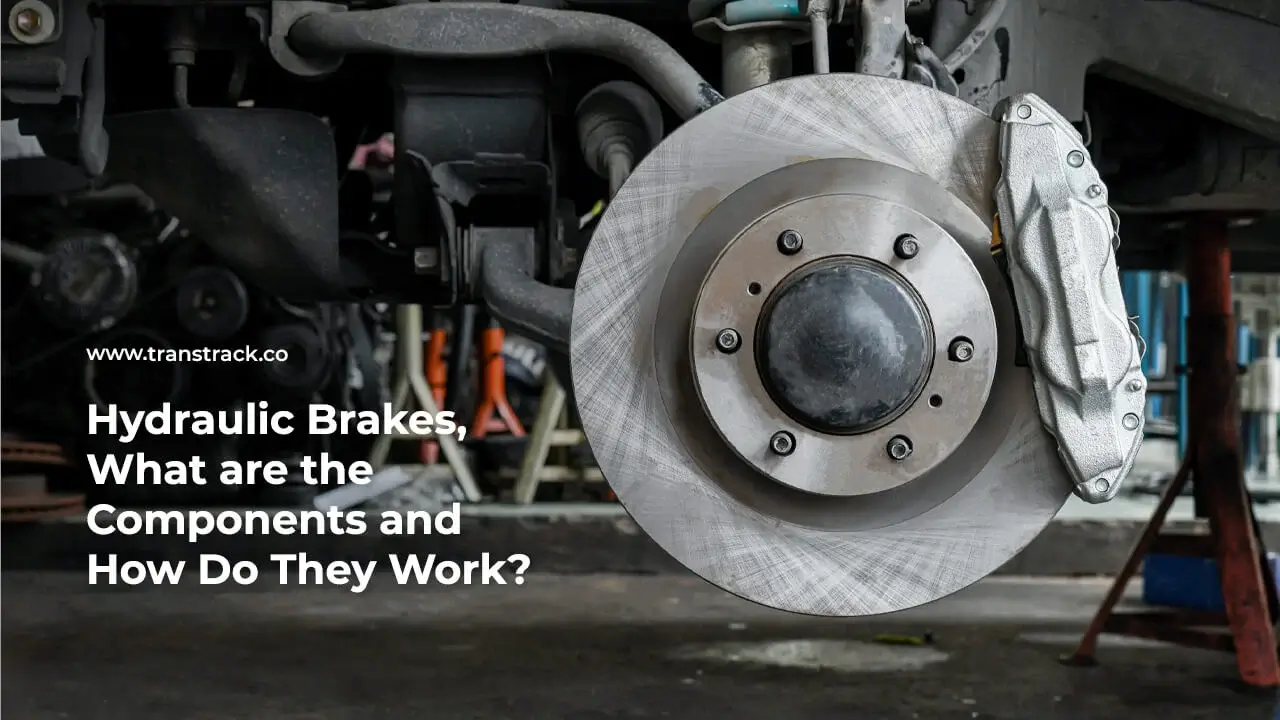
Hydraulic brakes are braking mechanisms that use brake fluid to transmit force into the system. The fluid transfers pressure from the control mechanism to the braking mechanism. The hydraulic braking system is widely used in low-speed four-wheelers. It works with the drum type, while the disc type is used in almost all cars.
It is also used on some bicycles. Single-acting hydraulic sacks are used in some front-wheel brakes, while double-acting hydraulic brakes are used in almost all situations.
In this type of braking system, the mechanical force transmitted by the driver on the brake pedal is converted into hydraulic pressure by a device known as a master cylinder, and then this hydraulic pressure is sent to the final drum or disk. This is to stop or accelerate the caliper vehicle.
This brake is a type of braking system widely used in cars with the application of hydraulic fluid. The working principle of a hydraulic braking system is entirely based on Pascal’s law, which states that the intensity of pressure inside a system enclosed by liquid is always the same in all directions.
A good and efficient braking system is an essential part of running systems like cars & engines. In general, in cars, different types of braking systems are used as needed because each type of braking system has its own applications and advantages.
What are the Functions of Hydraulic Brakes
Here are the functions of the hydraulic braking system in automotive systems:
- These brakes generate very high forces compared to mechanical braking.
- Final braking is fast and effective, which is why it is used on high-performance vehicles.
- The frictional wear that occurs in mechanical braking systems is much reduced to an optimum level in hydraulic braking systems.
- The chance of brake failure is reduced in hydraulic braking systems compared to mechanical types, due to the direct link between the actuator (brake pedal or lever) and the brake disc or drum.
- Hydraulic braking systems are very easy to repair due to their less complexity compared to mechanical brakes.
How Hydraulic Brakes Work
The way hydraulic brakes work is certainly different from mechanical braking systems that still use cables. In the hydraulic system, the braking system uses fluid. Not only that, the pedal model on these brakes is also different. Here you can see how these brakes work on cars and trucks.
How Hydraulic Brakes Work in Cars
The hydraulic system in a car works by using the basic principle of hydraulics, namely the principle of “equal pressure”. This system converts mechanical energy from the brake pedal into hydraulic pressure energy.
Here is how the hydraulic system works in a car:
- The brake pedal is depressed: When the brake pedal is depressed, pumping introduces brake fluid (usually dot 3 or dot 4) from the brake tank to this brake system.
- Pumping brake fluid: Pumping introduces brake fluid into the brake cylinder, which increases the pressure in the fluid.
- Pressure transmission: The pressure that is transmitted by the brake fluid to other parts of the brake system, such as the calliper and brake drum.
- Brake action: The calliper or brake drum uses hydraulic pressure to press and hold the wheel, bringing the car to a stop.
- Brake pedal released: When the brake pedal is released, the hydraulic pressure in the brake system will subside, allowing the wheels to turn again.
Hydraulic brakes are one of the most widely used types of brakes in automobiles due to their efficiency, responsiveness and reliability. This brake system is also easy to repair and expand, so it is widely used in various types and brands of cars.
How Hydraulic Brakes Work on Trucks
This brake system on trucks works on the same principle as in cars, namely by converting mechanical energy from the brake pedal into hydraulic pressure energy. Here is how the hydraulic brake system works on a truck:
- The brake pedal is depressed: When the brake pedal is depressed, pumping introduces brake fluid (usually dot 3 or dot 4) from the brake tank to the hydraulic system.
- Pumping brake fluid: Pumping introduces brake fluid into the brake cylinder, which increases the pressure in the fluid.
- Pressure transmission: The pressure that is transmitted by the brake fluid to other parts of the brake system, such as the calliper and brake drum.
- Brake action: The calliper or brake drum will use hydraulic pressure to press and hold the wheel, bringing the truck to a stop.
- Brake pedal released: When the brake pedal is released, the hydraulic pressure in the brake system will subside, allowing the wheels to turn again.
Hydraulic brake systems on trucks are usually larger in capacity and robust in design compared to hydraulic brake systems on cars, to cope with the heavier loads and higher speeds of trucks. This brake system is also very important to ensure that the truck can stop safely and efficiently in any condition.
Components of Hydraulic Brakes
In the process of working the system, this brake consists of various components that are interconnected with each other. There are at least 5 main components in the hydraulic braking system, including:
1. Brake Pedal/Brake Lever
The brake pedal or brake lever is also known as an input device because it is used to determine when the brakes will be activated and deactivated. In short, when the brake pedal is pressed, the brakes are activated. In this case, the pedal is responsible for applying pressure from the driver so that the brake hydraulic system can move.
2. Master Cylinder
The master cylinder is a component of the hydraulic system that functions to convert mechanical motion into hydraulic pressure. This conversion is useful because the working principle of this hydraulic system is to use the pressure of the fluid. Furthermore, the motion energy from the pedal will be transferred to hydraulic pressure by the master cylinder.
The master cylinder itself consists of a tube and a piston. The piston in this section is connected to the brake pedal which will then move back and forth in the tube. The movement of this piston will affect the space in the tube so that if there is fluid in the tube, the pressure will change following the movement of the piston.
3. Reservoir Tank
Reservoir tank is a component that serves to store brake fluid or brake fluid reserves to be used as a power supply. It works to avoid the risk of catching a cold that causes the brakes to fail.
‘Catching a cold’ is the term for when air enters the hydraulic system. When the air is compressed, the fluid pressure will increase, causing the brakes to deflate when pressed.
4. Hydraulic Pipe
Hydraulic pipes or hoses are components that function as a place for fluid or pressurized brake fluid to flow. Hydraulic fluid pressure is usually quite high so this hydraulic pipe must be made of special materials.
In braking systems there are usually two types of pipes, namely iron pipes and elastic pipes. But in general, this hydraulic pipe is made of metal so that it does not bend easily because the fluid pressure in the hose is quite high.
5. Brake Caliper/Actuator
The brake caliper or actuator functions to convert pressurized fluid energy back into a form of mechanical movement. This is so that the power can be used to move the brake lining so that it can press the brake disc.
Basically, almost all car braking systems today use hydraulic principles as their driving force. This type of braking system is easier to use, providing maximum safety.
Hydraulic brakes have several advantages, such as being responsive, efficient, easy to repair and expand, and have good and high reliability. However, just like any other braking system, these brake systems also require good care and maintenance to keep them functioning properly and ensure safe driving. Now, if you use Fleet Management System from TransTRACK, you can manage the use of vehicles in one system to create optimal work. Start using FMS from TransTRACK and take advantage of its main features!
Recent Post
Topic :