Pick and Pack Definition, Role, Challenges and Tips to Optimize it in Business Operations
Posted on January 2, 2024 by Nur Wachda Mihmidati
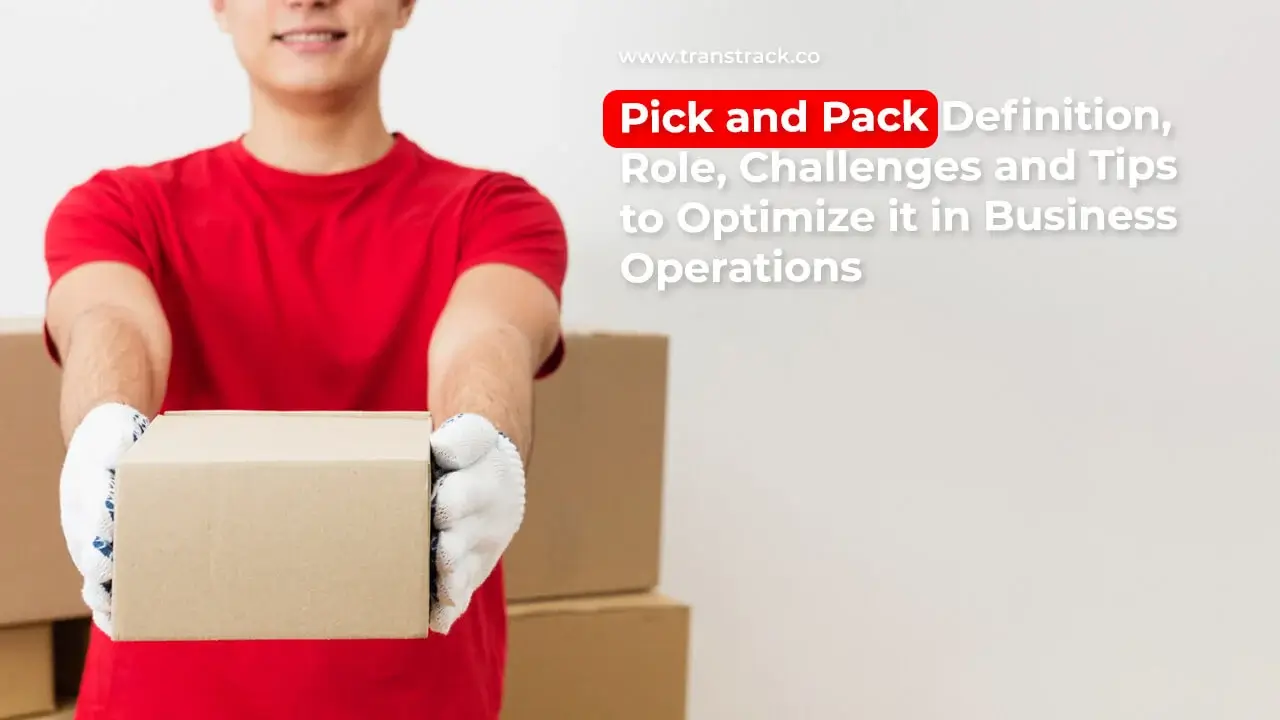
Pick and pack is one of the core activities in ensuring business operational efficiency. This process usually occurs after the goods have been stored in the warehouse. The pick and pack process is not only the core of inventory management, but also affects customer satisfaction.
Without a good pick and pack process, business operations in a company can be disrupted. How important is this process in business operations? What are the challenges like? With TransTRACK, let’s take a deeper look at the definition, role, challenges, and tips for optimizing this process in business operations.
Definition of Pick and Pack
Pick and pack are two important stages in the supply chain that involve the selection of items from warehouse stock (picking) and the packing process for shipment or distribution to customers. Essentially, this process is a critical step in ensuring that the products requested by customers are accurately collected and neatly packaged before being shipped.
It is important that this process is done quickly and accurately. This is because it directly affects customer satisfaction. Customers expect their orders to be delivered at the right time and with the right content. So, this process must be really considered to maintain the smooth operation of a business.
The Role of Pick and Pack in Business Operations
This process is more than just an essential element of warehouse management. It is the operational backbone that ensures smooth business operations and supply chain efficiency. Let’s discuss in detail the important role of these two crucial stages in business operations.
Ensuring Customer Orders are Served Quickly
One of the main roles of this process in business operations is to ensure that customer orders are served quickly and efficiently. In the picking stage, the warehouse team has the responsibility to identify and collect products according to customer orders. Once the picking process is complete, the packing step takes on an important role in ensuring smooth delivery. By ensuring good alignment between pick and pack, businesses can meet customer expectations related to fast and accurate delivery, creating a positive customer experience.
Reducing Delivery Errors
The role of pick and pack in reducing shipping errors cannot be overlooked. Accurate picking is the first step in avoiding shipping errors that can harm customers and damage business reputation. In addition, the packing process also plays a crucial role in reducing shipping errors. Careful packing that complies with operational standards can prevent product damage during shipping and ensure that the products received by customers are as expected. By reducing shipping errors, businesses not only maintain customer satisfaction but also avoid additional costs associated with returns and replacement items.
Improves Delivery Accuracy and Speed
This process also directly improves delivery accuracy and speed. By using advanced technologies such as integrated warehouse management systems, companies can track inventory in real-time, ensuring that products listed in customer orders are still available and can be collected quickly. Increased delivery speed can also be achieved through optimizing the packing process. Using efficient packaging methods and appropriate packaging can shorten the preparation time for shipments.
Challenges in the Pick and Pack Process
Challenges in this process involve a number of complexities that can affect the overall operational efficiency of the business. Problems that often arise are stock uncertainty and fluctuations in customer demand. Poorly managed inventory can result in difficulties in determining the exact location of the items to be picked, thus slowing down the overall process.
Furthermore, human involvement in this process also carries a significant risk of error. Picking errors, such as picking the wrong item or the wrong quantity, can cause delays and additional costs in delivery. Therefore, key challenges in this process involve reducing stock uncertainty, improving human precision, and increasing system flexibility to respond more effectively to market changes.
Tips for Optimizing the Pick and Pack Process
In order for this process to run more smoothly, it is necessary to optimize the process. Here are some tips that can be applied:
Process Automation
Implementing automation technology in the picking and packing process can increase speed and reduce errors. Automated picking systems and packaging machines can help improve efficiency significantly.
Employee Training
Providing adequate training to employees involved in this process is essential. Skilled employees can ensure accuracy and efficiency in carrying out their tasks.
Analyze Data for Continual Improvement
Analyzing operational data on a regular basis can help identify areas that require improvement. With a better understanding of process performance, companies can continuously improve pick and pack efficiency.
This process is not just about collecting and packing goods. It is the foundation of the overall customer experience and supply chain integration. By understanding its critical role, companies can better face challenges and continuously optimize processes to achieve higher levels of efficiency.
The implementation of Logistic Service Integrator (LSI) technology from TransTRACK significantly optimizes the pick and pack process in operational management. With advanced features such as real-time visibility of inventory, better coordination between picking and packing teams, and data integration between departments, LSI ensures high operational efficiency. The system enables automation in item selection, speeds up the picking process, and reduces the risk of human error.
With the adoption of this technology, companies can increase productivity, reduce errors, and provide a better customer experience through a more efficient and well-managed pick and pack process.
Recent Post
Topic :