Outbound Logistics, What is the Process and Examples of Activities?
Posted on December 4, 2023 by Nur Wachda Mihmidati
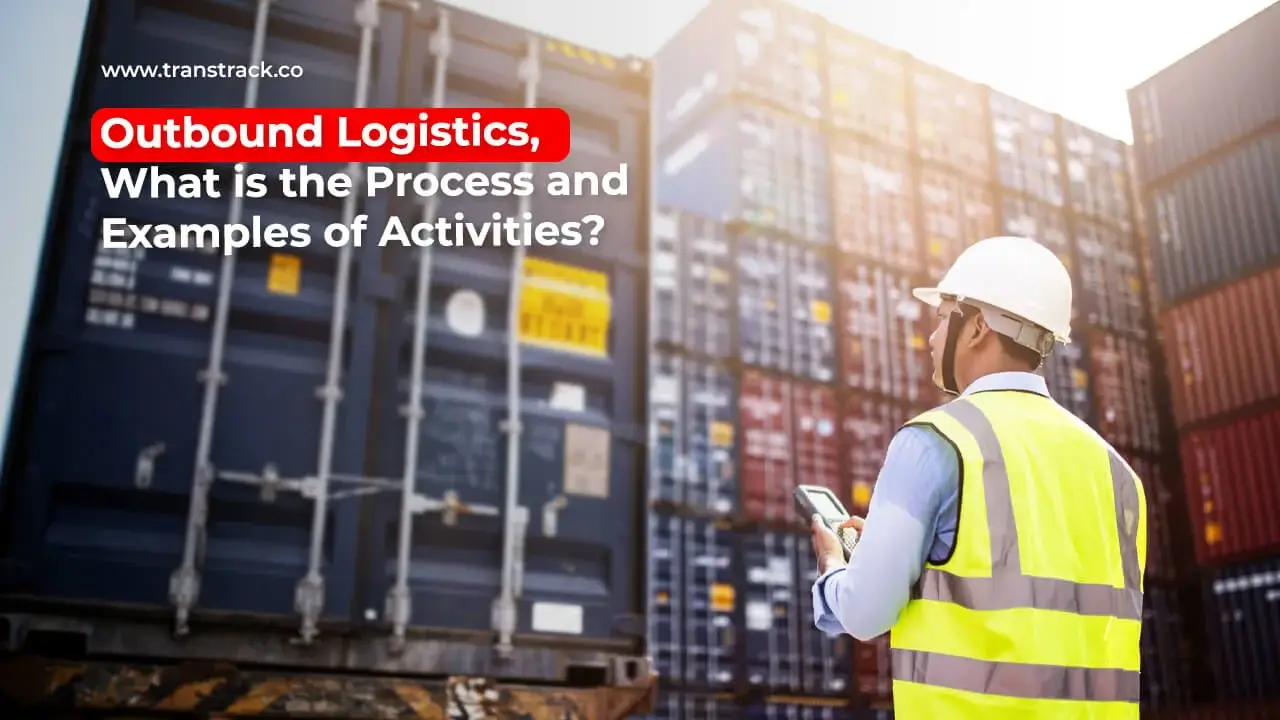
Outbound Logistics is the activity from the production or collection of goods to their delivery to customers. This includes monitoring production, collecting the required amount of inventory, picking and packing orders according to accurately generated and processed invoices, and managing the flow through various shipping options. Running these Outbound Logistics activities effectively is crucial to your organization’s success.
Outbound Logistics and Inbound Logistics work together but have different roles. Inbound Logistics processes include the movement of raw materials, finished goods, and supplies from manufacturers or other distribution channels to warehouses or retail stores. Outbound Logistics processes deal with the processing and transportation of products to consumers. The Outbound Logistics process usually starts at the distribution center and ends when the order reaches its final destination.
Choosing the right Outbound Logistics system according to your organization’s needs will automate the process with fewer errors and more accurate access to factors that affect the results. Outbound Logistics systems also help pinpoint potential errors and allow users to navigate back to see how to correct mistakes. The system will guide faster and more accurate deliveries when routing orders to trailers. Logs will be created, and data can be compiled and accessed for future reference electronically.
Outbound Logistics Process
Outbound Logistics addresses the last stage of the supply chain, which starts at the warehouse and ends with the delivery of the order to its destination.
Selecting the Menu
This is one of the core activities of any logistics facility. Order processing is an operation in charge of preparing products requested by customers to be shipped in the form of orders. These can be shipped to end customers, to distribution centers, or to other companies’ warehouses and stores. One of the main goals of outbound logistics is to deliver the highest number of orders at the minimum cost and in the shortest possible time.
Order Consolidation
This consists of organizing and sorting orders before shipping them, grouping them by final destination. The order consolidation process usually takes place in an area specialized for this purpose or directly in a consolidation warehouse. In facilities that ship full pallets, goods are usually sorted in front of the loading dock, based on the order or transportation route. But for businesses that distribute small items, the products are grouped in a consolidation area. The purpose of this operation is to lower the shipping and delivery costs for each order while reducing unnecessary trips in the warehouse.
Packing and Labeling
Packing refers to conditioning and packaging an order for onward shipment. At this stage, the type of packing material is selected based on the size, quantity, and distinctive features of the product. A shipping label is placed on the outside of each box, containing the order reference number, destination address, and, sometimes, its track number. The label also contains a barcode that, once scanned, accesses information related to the shipment, ensuring product traceability.
Truck Loading
This process involves placing products on trucks to transport them to their destinations (distribution centers, other warehouses, or directly to end consumers). To guarantee efficient truck loading, it is important to group orders by transportation route and distribute goods based on their weight and volume. Proper truck load planning is essential in Outbound Logistics because once the order is on the vehicle, it is very difficult to undo mistakes.
Booking Transportation and Shipping
Last mile management – the last part of the freight shipping process – is one of Outbound Logistics’ main challenges. From the moment they leave the last distribution point until they reach their final destination, packages face many obstacles. Some of these obstacles are related to the transportation itself, while others stem from the type of product being shipped. Optimizing costs at this stage can be the key to standing out from your competitors and having a productive and effective Outbound Logistics operation.
In brief, the process of Outbound Logistics is as follows:
- Customer Order A customer places an order through one of the channels through which the company sells its offerings.
- Order Processing The company validates the order, receives the quantity and products requested from inventory and generates documentation.
- Inventory Replenishment Reserve moves into primary storage, replacing purchased products. This process may trigger the production of more goods or the ordering of raw materials from suppliers to maintain adequate inventory levels.
- Picking Warehouse workers pick products from storage to fulfill orders.
- Packing, Staging and Loading Staff pack, label and document orders according to internal and customer requirements. Workers sort orders according to shipping mode, delivery speed or destination. The team loads orders onto outbound trucks.
- Delivery and Documentation The order leaves the warehouse for the distribution center or partner. The company’s system records the shipment and sends the customer tracking details.
- Last Mile Delivery The order is sent from the distribution center to the customer. This can be the most expensive and the most important step.
Examples of Outbound Logistics Activities
Any business that makes products or provides services must know how to manage logistics. For example, companies that turn silicon into computer chips or farmers who grow wheat from seed use logistics to deliver goods to their customers.
Customer Orders
For example, a national boutique chain, Picture Perfect, has 37 stores. The company orders a collection of women’s pants, blazers, skirts, blouses, dresses and scarves in various quantities in women’s sizes 0 to 18 on the Sorina website. Picture Perfect uses internal data on shopper preferences, past sales and trend forecasts to determine the quantity of each product and size to purchase. Sorina staff need to pay attention to the details of the order due to variations in patterns (paisley and chevron), colors (burgundy and blue) and sizes. Sending the wrong items or quantities can result in customer complaints and lost sales for products that do not arrive in time for seasonal shopping.
Order Processing
Sorina’s order processing team checks Picture Perfect’s order by confirming that Sorina has the correct quantity, size, garment type and color. They send the order confirmation to Picture Perfect. Sorina’s inventory management system allocates these items so that the clothes are no longer available for sale to others. The system sends order manifests and picking tickets to the warehouse.
Replenishment
Workers move clothes from remote storage to the shipping warehouse to replace purchased products as needed. Planner Sorina noted that a particular blazer was selling faster than expected and asked the garment maker to sew more.
Picking
Warehouse staff use a zone strategy to select clothes for multiple orders. Workers hang a Picture Perfect blouse, for example, on an electric clothes rack along with blouses that are part of orders from two other retailers. They use barcodes to differentiate the orders.
Packing, Staging, and Loading
All clothing items in Picture Perfect’s order assemble at the packing station. A staff member scans the barcode on the hanger to ensure that the order is correct. The packer packs the order with tissue, so that the clothes do not wrinkle. They put the boxes together on a pallet, shrink-wrap the pallet, and affix the destination and manifest labels. The packers split Picture Perfect’s order into two batches, one for its distribution center in the West and the other for its distribution center in the East. Each joins other orders heading in the same direction with similar service levels. Picture Perfect orders will be shipped via ground shipping as the delivery is not rushed. Workers load pallets onto an outbound truck.
Delivery and Documentation
The order departs. The Sorina system records the shipment and sends tracking information to Picture Perfect’s purchasing department. The Sorina system also sends arrival information to the network distribution center.
Difference between Inbound and Outbound Logistics
Inbound Logistics and Outbound Logistics aim to accomplish different things. The goal of Inbound Logistics is to secure supply for the business, while the goal of Outbound Logistics is to meet and fulfill demand.
Inbound Logistics and Outbound Logistics processes also move and deliver different goods to different parties. Inbound Logistics processes move inventory, raw materials, or supplies from suppliers to businesses; Outbound Logistics, on the other hand, moves finished products from businesses to customers or end users.
The comparison table below shows the differences between the Inbound Logistics Outbound Logistics process.
Inbound | Outbound | |
Definition | The process involved in moving materials or goods into the supply chain, and securing inventory that your business will later sell. | Processes involved in moving finished inventory from the supply chain by fulfilling and delivering orders to end customers. |
Process | – Material management- Sourcing- Warehouse receiving- Inventory storage | – Order confirmation & processing- Picking- Packing- Shipping – Long distance shipping- Customer service involving shipping |
Touchpoints | Transported From:- Suppliers- Manufacturers- Distributors- Product HoldersShipped To: -Company-Brand-Retailer-Third party logistics company | Shipped From:- Company- Brand- Retailer- Third party logistics companyDelivered To: – End customer End user |
Outbound Logistics is what is usually done if you order goods with a tracking report that the delivery service has provided. Well, for those of you who have a company with goods delivery services, or if you have another business with a large number of fleets, you can use the Fleet Management System from TransTRACK. This FMS will help you manage a large number of fleets to keep track in real time. Plus, you will get top-notch security features when you start using FMS. Start using Fleet Management System from TransTRACK and optimize your fleet management!
Recent Post
Topic :