Types, Components, How to Calculate, and Save on Operating Costs
Posted on October 9, 2023 by Nur Wachda Mihmidati
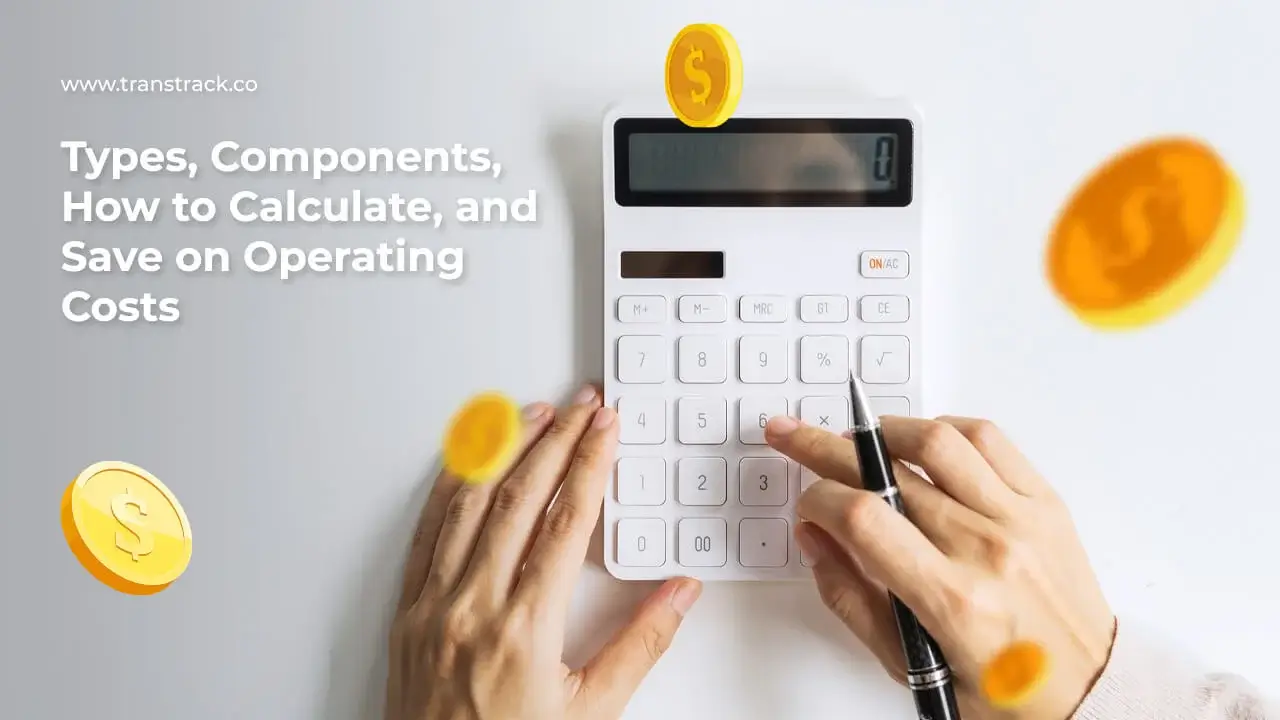
Operating expenses, also known as operating costs or operational expenditure (OPEX) in English, refer to the costs associated with the day-to-day running of a business or organization. These costs are incurred to keep a company’s routine operations and activities running smoothly.
Operating costs are opposed to capital expenditure (CAPEX), which includes long-term investments in physical assets such as land, buildings, production equipment, and new technology. Operating expenses are recurring costs related to day-to-day operations, while capital expenses are long-term investments typically used to improve or expand a business. Find out more through the following article TransTRACK!
Type of Operating Expenses
Operating costs can be divided into two main categories based on their nature: Fixed Cost and Variable Cost. Here’s a brief explanation of these two types of costs:
Fixed Cost
- Fixed costs are operating costs that do not change regardless of how many products are produced or services are provided by the company.
- Examples of fixed costs include leases or mortgages of offices or production facilities, salaries of permanent employees, insurance, and interest costs on fixed loans.
- Fixed costs do not depend on the level of production or sales, and they remain constant over a period of time.
Variable Cost
- Variable costs are operating costs that change as production or sales levels increase or decrease.
- Examples of variable costs include raw materials used in production, production wages paid per unit of production, packaging material costs, and distribution costs.
- Variable costs increase when production or sales increase and decrease when production or sales decrease.
Cost classification is important in financial planning and business management. A company must understand the composition of its operating costs, including what percentage of costs are fixed and variable, as this will affect the calculation of net profit, break-even point, and overall profit. In decision-making, a company should also consider how changes in production or sales volume will affect its operating costs.
Operating Cost Components
Operating cost components can be grouped into two main categories: Direct Costs and Indirect Costs. In addition, these costs can be further divided into Production Costs and Non-Production Costs. A brief explanation of each component follows:
Direct Costs
- Direct costs are costs that are directly related to the production or provision of goods or services. These costs are directly attributable to a specific product or service.
- Examples of direct costs include raw materials, direct wages (wages of workers involved in production), and costs directly related to specific production, such as direct labor and raw materials used to make a product.
Indirect Costs
- Indirect costs are costs that cannot be directly attributed to a specific product or service. They are generally related to the overall operations of the company.
- Examples of indirect costs include electricity costs for the entire facility, administrative staff salaries, administrative costs, and operating costs that cannot be directly identified with a specific product or service.
Production Costs
- Production costs are costs directly related to the process of producing goods or services. It includes direct costs, such as raw materials and direct wages, as well as production overhead costs associated with production.
- Production overhead costs can include equipment costs, depreciation, production auxiliary materials, production energy costs, and machine maintenance costs.
Non-Production Costs
- Non-production costs are costs that are not directly related to the production of goods or services. This includes the costs of administrative, marketing, distribution, and other business functions that are not involved in the physical production of the product.
- Examples of non-production costs include sales and marketing costs, general administrative costs, research and development costs, and general and administrative costs.
Understanding these operating cost components is important for companies to manage and control their expenses, determine product or service prices, and calculate net profit margins. It also helps in business planning and strategic decision-making.
How to Calculate Fleet Operating Costs
Calculating fleet operating costs is an important step in fleet management, especially if you have a fleet of vehicles or equipment used in your business operations. Here are the general steps you can follow to calculate fleet operating costs:
Identification of Cost Components
- Determine all relevant cost components associated with your fleet. This may include the cost of fuel, maintenance, insurance, credit payments, storage fees, taxes, and other administrative costs related to the fleet.
Cost Grouping
- Group those costs into two main categories: variable costs and fixed costs. Variable costs, such as fuel, will change based on fleet usage, while fixed costs, such as annual insurance, remain constant over a period of time.
Calculating Variable Costs
- For variable costs, such as fuel, take note of the amount of fuel used by each vehicle in the fleet over a period of time. You can use refueling records or a fleet tracking system if you have one. Then, multiply the number of liters or gallons of fuel used by the price per liter or gallon to get the total fuel cost.
Calculating Fixed Costs
- Fixed costs such as insurance, taxes, and credit payments can be divided into a cost per unit of the fleet. For example, for annual insurance costs, divide the amount by the number of vehicles in the fleet to get the insurance cost per unit.
Add All Cost Components
- Add up all the variable and fixed costs to get the total operating cost of your fleet over a period of time.
Calculate Cost per Unit
- To get the operating cost per unit, divide the total operating cost by the number of vehicles in the fleet.
Analysis and Planning
- After calculating operational costs, analyze the results. This can help you understand how efficiently your fleet is operating and whether there is room for savings or improvement. Additionally, you can use this information to calculate daily, monthly, or annual operating costs.
It is important to note that effective fleet management involves constant monitoring and analysis, as fleet operating costs can change over time and changes in business operations. In addition, fleet tracking technology and fleet management software can help you automate the collection of operational cost data and its analysis.
How to Save on Fleet Operating Costs
TransTRACK is one of the companies that provide Fleet Management System (FMS) solutions that can help in managing and optimizing fleet operational costs. Here’s how you can save on fleet operating costs by using a Fleet Management System solution from TransTRACK or a similar provider:
Fleet Performance Monitoring
- Use FMS solutions to track the performance of every vehicle in your fleet. You can monitor how efficient vehicles are in terms of fuel consumption, travel time, and driver patterns. Identify vehicles that may require more intensive maintenance or updates.
Travel Route Optimization
- FMS solutions usually come with route planning features that can help you optimize travel routes. This can reduce the mileage and time required to complete tasks, reduce fuel consumption, and save on operational costs.
Fuel Savings
- Use the data collected by the FMS to monitor fuel usage. Identify inefficient fuel use or leaks. Based on this analysis, you can take corrective actions, such as driver training or better routine maintenance.
Preventive Maintenance
- Use the information provided by the FMS to organize preventive maintenance on a scheduled basis. This will help avoid major breakdowns and reduce unexpected downtime.
Driver Management
- Monitor driver behavior, such as speed, acceleration, and aggressive braking. FMS can help you train drivers to drive more efficiently, which can save fuel and reduce repair costs.
Speed Control
- Some FMS solutions have a function to limit vehicle speed. This can help reduce fuel consumption and the risk of accidents.
Inventory Management
- Use FMS solutions to track inventory and stock usage in your fleet. This helps avoid loss or unrecorded usage.
Integration with Financial Reporting System
- Integrating FMS solutions with your financial reporting system makes it easy for you to monitor fleet operating costs and make decisions based on accurate data.
Driver Training
- Use data from the FMS to organize appropriate driver training to improve driver awareness and operating efficiency.
Periodic Monitoring and Maintenance
- Make sure your FMS system is operating properly and the hardware is functioning properly. Performing regular maintenance on the system will help maintain accurate and reliable data.
With the help of Fleet Management System solutions such as those provided by TransTRACK, you can automate many aspects of fleet management and optimize your operations, which in turn will help you save on fleet operating costs. Make sure to utilize the various features and functionalities provided by such solutions to achieve the best results.
In managing your vehicle fleet, controlling operational costs is a critical step to improving the profitability of your business. TransTRACK’s Fleet Management System Fleet Management System solution is the key to achieving efficiency and significant savings in your fleet operations.
With TransTRACK, you can:
- Monitor vehicle performance in real-time.
- Optimize travel routes and reduce fuel consumption.
- Perform timely preventive maintenance.
- Control driver behavior for efficiency and safety.
- Conduct efficient inventory management.
- Get accurate reports for better decision-making.
With the help of TransTRACK, you can save on operational costs, increase fleet productivity, and ensure driver safety. Don’t let fleet operational costs hamper your business growth. Try TransTRACK now to optimize your fleet operations and increase your profits. Contact us for a demo and more information!
Take the next step towards more efficient and cost-effective fleet management with TransTRACK. Click here to start your journey towards operational cost savings and greater business success.
Topic :