Inventory Control: its Functions, Tasks and Activities
Posted on November 29, 2024 by Nur Wachda Mihmidati
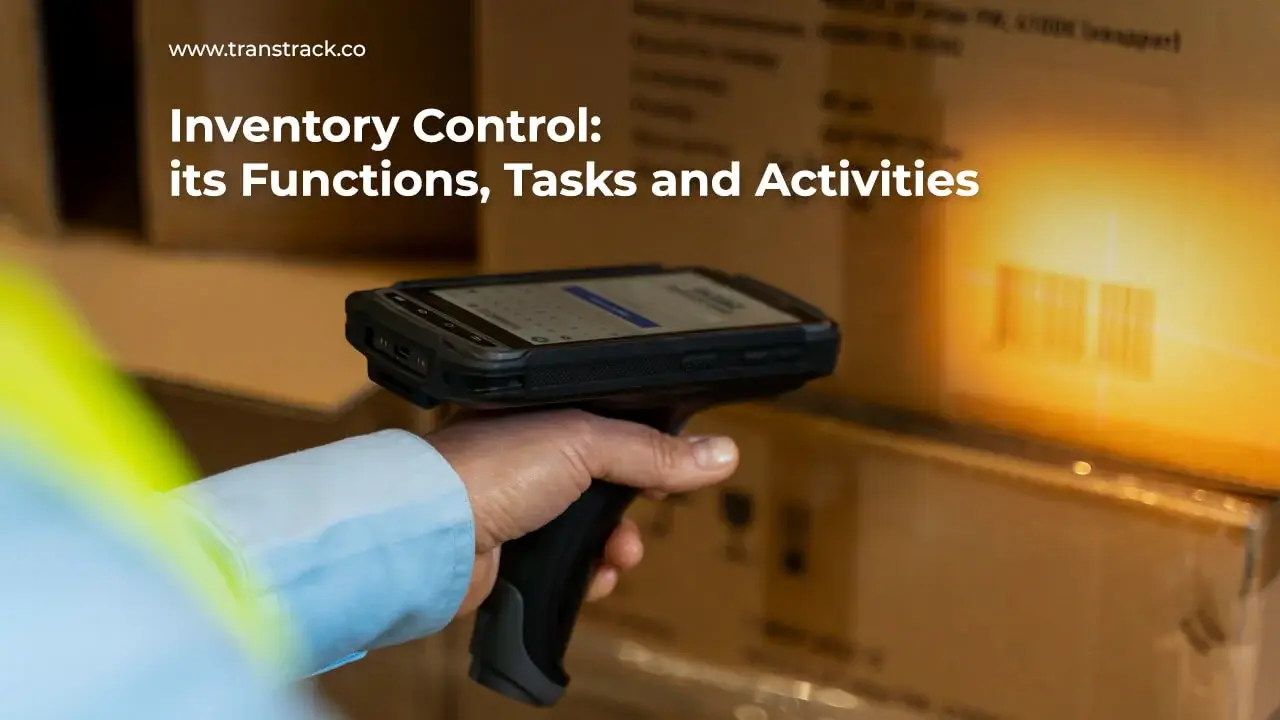
Inventory control or stock control is the process of managing and monitoring the stock or products within a business or organization. Its goal is to ensure that inventory is always available in sufficient quantities to meet customer demand while avoiding excess inventory and unnecessary costs.
In practice, this activity involves collecting data on inventory and customer demand and using statistical analysis and other techniques to predict future inventory needs. This enables companies to make informed decisions about when to reorder more products, when to adjust prices, and how to manage inventory effectively.
In practical terms, this activity also involves the use of specialized software that can automate inventory management and provide accurate information on available inventory, pending orders, and upcoming inventory.
What are the Tasks of Inventory Control?
The primary task of this activity is to manage the inventory of goods/services in a company or organization. This involves monitoring the quantity of available stock, the timing and frequency of procurement, and how to optimize inventory to meet customer demand without unnecessary excess.
Another task of inventory control is to develop an effective and efficient inventory control system, including pricing methods, procurement of goods, inventory planning, and monitoring stock usage. This activity is also responsible for ensuring the accuracy of inventory data and maintaining the quality of stored goods/services.
In general, the tasks of this activity aim to ensure an adequate supply of goods/services to meet customer demand while minimizing the costs and risks associated with excess or insufficient inventory. Here are some points about the tasks of Inventory Control:
Counting the quantity of inventory in the warehouse
This activity must regularly count the number of goods or products available in the warehouse to ensure that inventory is always available in sufficient quantities and meets customer needs.
Checking data
Inventory control must ensure that data regarding inventory, such as prices, quantities, and availability, are recorded accurately and kept up-to-date.
Conducting periodic audits
Inventory control must conduct periodic audits of inventory to ensure that the quantities recorded in the system match the physical quantities in the warehouse.
Generating reports
This activity must generate reports on the status of inventory, including information on incoming and outgoing goods, available inventory, and forecasts of future inventory needs. These reports can help management make informed decisions about inventory management in the future.
Inventory Control Method
Inventory control methods are approaches used to manage inventory with the aim of maintaining a balance between demand and supply and minimizing the costs associated with storing and procuring goods. Here are some common methods used in inventory control:
1. FIFO (First In, First Out)
- The first item in is the first item out. Suitable for time-sensitive items, such as food.
- Advantages: Avoid expired items.
- Weaknesses: Not effective for durable goods.
2. LIFO (Last In, First Out)
- The last item in is the first item out. Used for goods with fluctuating values.
- Advantages: New items are used more often.
- Weaknesses: Old items may accumulate.
3. JIT (Just In Time)
- Organizes procurement of goods only when needed, reducing storage.
- Advantages: Reduced storage costs.
- Weaknesses: Vulnerable to supply disruptions.
4. Economic Order Quantity (EOQ)
- Determines the optimal order quantity to minimize ordering and storage costs.
- Advantages: Establishes efficient ordering.
- Weaknesses: Relies on assumptions that are not always accurate.
5. Reorder Point (ROP)
- Sets the reorder point to avoid running out of stock.
- Advantages: Ensures sufficient supply.
- Weaknesses: Requires careful monitoring of inventory.
6. Perpetual Inventory System
- Real-time inventory recording, every transaction is recorded immediately.
- Advantages: Up-to-date and accurate information.
- Weaknesses: Requires an advanced software system.
7. Periodic Inventory System
- Inventory counts are done at specific periods.
- Advantages: Simple and cheap.
- Weaknesses: Does not provide up-to-date data.
Each method has advantages and disadvantages, so it is important to choose according to the needs and characteristics of the company.
Benefits of Inventory Control for Businesses
Inventory Control provides significant benefits to businesses, here’s the list:
Real-Time Reporting
With effective stock control, a company can monitor its inventory in real-time. It allows businesses to know the quantity of stock available at any given moment and make decisions based on the latest and most accurate information. Consequently, businesses can avoid inventory shortages or excesses that can impact profits and losses.
Ensuring Safe Inventory
Stock control helps businesses maintain an adequate inventory, ensuring that they can meet customer demands at the right time. This can prevent the loss of customers due to inventory shortages and reduce the costs of storing unnecessary inventory.
Informed Decision-Making
Stock control provides accurate and up-to-date information about inventory. This information can be used by management to make informed business decisions, such as when to order goods or when to reduce inventory levels. With accurate and current information, management can make better decisions and optimize inventory effectively.
In conclusion, this activity can help businesses minimize inventory costs, improve customer satisfaction, and enhance overall operational efficiency.
Functions of Inventory Control
The functions of stock control involve managing the inventory of goods/services within a company or organization. Here are some more detailed functions of inventory control:
Inventory Counting
Stock control is responsible for counting the quantity of goods/services available at a specific time. This enables businesses to know when to order new goods and avoid inventory shortages that can affect customers and profits.
Forecasting
Stock control estimates the quantity of goods/services needed to meet customer demand within a specific timeframe. These forecasts help businesses prepare their inventory and avoid shortages or excess inventory.
Ordering
Stock control places orders for new goods or arranges the delivery of already ordered goods. This involves selecting the right suppliers, determining prices, and scheduling deliveries.
Monitoring Inventory
Stock control regularly monitors inventory to ensure that it is sufficient. This involves checking existing inventory, managing expired or damaged products, and removing unnecessary items.
Managing Disposal
Stock control is also responsible for managing the disposal of goods that are no longer needed or damaged. This includes deciding when to dispose of items and how to do so safely and efficiently.
Ensuring Data Accuracy
Stock control ensures that inventory data is accurate and up-to-date. This enables businesses to make informed decisions based on accurate data and avoid inventory shortages or excesses.
In conclusion, the functions of this activity are designed to ensure an adequate supply of goods/services to meet customer demand while minimizing costs and risks associated with excess or insufficient inventory.
What Are the Activities of Inventory Control?
Here are some common activities of Inventory Control carried out in a company or organization:
Stocktaking
This is the process of physically counting the inventory of goods at a specific point in time. Stocktaking is done to ensure that the recorded inventory matches the physical inventory, minimizing recording errors and avoiding business losses.
Cycle Count
This involves regularly counting a specific quantity of inventory items. This process allows companies to monitor inventory periodically and ensure the accuracy of recorded inventory.
Audit – Movement
This process involves checking items that have been moved from one location to another within the warehouse or during the production process. The goal is to ensure accurate transfers without loss or damage to items.
Audit – Putaway:
This process involves inspecting items that have just been stored in storage locations or on shelves by warehouse workers. The aim is to ensure that items are placed in the correct location without any damage or loss.
Audit – Picking
This process involves checking items taken from storage locations or shelves by warehouse workers to fulfill customer orders. The goal is to ensure that the correct items are picked and the quantities match the customer’s order.
Overall, the activities of inventory control aim to ensure accurate record-keeping of inventory and meet business needs. These processes minimize recording errors, prevent loss or damage to items, and enhance overall efficiency and productivity.
Difference Between Inventory Control and Inventory Management
Although often used interchangeably, Inventory Control and Inventory Management differ in terms of focus and scope of responsibilities. Here are the differences between Inventory Control and Inventory Management:
Focus
Inventory Control focuses on inventory control and supervision aspects. It includes actions to minimize inventory costs, avoid excess or insufficient inventory, and optimize short-term inventory availability. On the other hand, Inventory Management focuses more on long-term inventory planning and management strategies. It involves actions to ensure sufficient inventory availability to meet customer demand, manage risks, and enhance business efficiency and profits.
Scope of Responsibilities
Stock control typically encompasses operational tasks such as counting inventory, placing orders, monitoring inventory, and disposing of unnecessary items. Meanwhile, Inventory Management includes more strategic tasks like inventory planning, developing inventory management strategies, monitoring customer demand trends, and determining pricing policies.
Objectives
The objective of stock control is to control inventory in the short term and ensure sufficient inventory availability to meet customer demand. Conversely, the objective of Inventory Management is to ensure the right inventory in the right quantity, at the right time, with minimal costs, and optimize value-added benefits for the business.
In conclusion, Inventory Control and Inventory Management differ in terms of focus, scope of responsibilities, and objectives. However, both are crucial for businesses to effectively and efficiently manage inventory.
In managing inventory, one essential aspect is ensuring that items are consistently available and well-managed. One solution to facilitate inventory management is by using the Fleet Management System from TransTRACK.
TransTRACK’s Fleet Management System also comes with features such as inventory cost calculation, delivery scheduling, and comprehensive reporting. This enables companies to make better decisions based on accurate and reliable information.
If you want to optimize inventory management in your company, consider trying TransTRACK’s Fleet Management System. By using this system, you can improve efficiency, reduce costs, and enhance overall business profits. Contact TransTRACK now for more information!
Recent Post
Topic :