Heavy Equipment Productivity Calculation: How to Optimize Performance in the Field
Posted on May 20, 2025 by Nur Wachda Mihmidati

In the construction, mining, forestry, and logistics industries, heavy equipment plays a crucial role in supporting smooth operations in the field. However, having heavy equipment is not enough-it’s more important how productive it is when in use. Therefore, machine productivity calculations are key in planning work schedules, managing costs, and ensuring overall project efficiency.
This article TransTRACK will comprehensively discuss the basic formula of machine productivity, the factors that affect it, and optimization tips to achieve maximum work results.
What is heavy equipment productivity?
Machine productivity is a measure of the efficiency of a machine’s performance in completing a job within a certain period of time. In general, productivity is calculated as the amount of output produced by a machine per unit of time, such as per hour or per day.
Why is productivity calculation important?
Machine productivity calculations are important because they serve as the basis for project planning, control, and evaluation, especially on projects that involve earthworks, construction, forestry, mining, or plantations.
Here are the main reasons why productivity calculation is important:
1. Project Time and Schedule Planning
By knowing the productivity of the machine, the project manager can estimate:
- How long the job will take to complete.
- The number of tools needed to achieve the target time.
Example: If it is known that one excavator can dig 100 m³ per hour and the volume of soil to be excavated is 1,000 m³, then the work can be completed in 10 hours (with 1 excavator).
2. Cost Planning and Budget Efficiency
Productivity affects direct costs, such as:
- Machine rental costs
- Fuel and maintenance costs
- Labor costs
Lower productivity = longer working time = higher operating costs.
3. Selection of the Right Type and Number of Tools
With productivity data, the engineer or project planner can choose:
- The most efficient type of machine for a particular type of work.
- Combination of equipment (e.g. excavator to dump truck ratio) to avoid idle time.
4. Performance Evaluation and Problem Identification
A comparison between actual productivity vs. planned productivity can show:
- Is the work going according to plan?
- Are there any delays or problems in the field?
This helps management make adjustments or improvements quickly.
5. Improving Operational Efficiency
By understanding the factors that affect productivity, companies can:
- Provide operator training
- Schedule equipment maintenance more efficiently
- Improve coordination between work units
Productivity calculation = the basis for efficiency, effectiveness, and profitability.
Without proper calculations, projects risk wasting time, costs, and resources.
What are the factors that affect heavy equipment productivity?
Here is an explanation of factors that affect heavy equipment productivity, specifically for types such as excavators, bulldozers, dump trucks, loaders, and cranes:
1. Types of Heavy Equipment
Each machine has different functions and work capabilities, which affect productivity:
- Excavator: Productivity is affected by bucket capacity, cycle speed and working range.
- Bulldozer: Depends on blade size, thrust, and pushing surface conditions.
- Dump Truck: Load capacity, travel speed, and loading and unloading time are highly influential.
- Loader: Influenced by bucket capacity, tool maneuverability, and loading time.
- Crane: Productivity depends on lifting capacity, boom reach, and lifting speed.
2. Field Conditions
Field factors greatly affect the smooth operation of the machine:
- Topography: Steep slopes or hilly terrain can reduce work efficiency and speed.
- Soil type: Hard, rocky or muddy ground may affect the speed and safety of the operation.
- Weather: Heavy rain, fog, or extreme heat can hinder equipment or make terrain slippery and risky.
3. Operator Quality
People remain a major factor in productivity:
- Work experience: Experienced operators know how to work faster and more efficiently.
- Technical skills: The ability to smoothly operate tools, avoid damage, and perform complex maneuvers.
- Discipline and safety: Orderly operators tend to maintain work continuity without downtime due to accidents or errors.
4. Machine Condition
Excellent equipment will result in maximum productivity:
- Machine performance: Engine in top condition runs faster and more stable.
- Tire/chain condition: Worn tires or loose chains decrease traction and increase fuel consumption.
- Regular maintenance: Maintained tools avoid downtime due to sudden breakdowns.
5. External Factors
Factors outside the tool and operator that also have an effect:
- Coordination between tools: For example, the ratio of excavator to dump truck should be appropriate so that there is no waiting time.
- Project management: Good planning will minimize downtime and confusion in the field.
- Operational disruptions: Such as fuel supply delays, shift changes, or heavy equipment queues.
- Regulations and permits: Sometimes operations have to stop due to inspections or restrictions on working hours.
Machine productivity is the result of a combination of tool specifications, field conditions, operator quality, tool readiness, and work coordination. Optimizing all these factors will result in work efficiency and project cost savings.
Heavy Equipment Productivity Calculation Formula
The following is an explanation of the heavy equipment productivity calculation formula, complete with basic formulas and special formulas for excavators and dump trucks, as well as a description of its components:
Basic Formula for Heavy Equipment Productivity
- Common units: m³/hour or ton/hour
Productivity Formula for Excavators
Component Explanation:
- Bucket Capacity: Size of bucket contents (e.g. 1.2 m³)
- Cycles per hour: How many work cycles are performed in 1 hour (e.g. 120 cycles)
- Tool efficiency: Percentage of effective working time (usually between 70-85%)
- Correction factor: Correction due to swell factor, spillage, and working conditions (e.g. 0.9)
Calculation Example:
- Bucket capacity: 1,2 m³
- Cycles per hour: 120
- Efficiency: 0,8
- Correction factor: 0,9
Productivity Formula for Dump Truck
Explanatory Component:
- Payload Capacity: Effective carrying capacity of the dump truck (e.g. 15 tons)
- Number of Trips/Hour: Number of transportations per hour (based on travel time + loading and unloading)
- Tool efficiency: Generally 0.7-0.9 depending on field conditions
Calculation Example:
- Load capacity: 15 tons
- Number of trips/hour: 3 trips
- Tool efficiency: 0,85
Additional Notes:
- Swell Factor: Used to correct the volume of disturbed soil (used in earthworks).
- Bucket fill factor: Correction if the bucket is not always fully filled (generally 0.8-0.95).
- Cycle Time : The total time of one work cycle (dig – haul – dump – return).
Tips for Optimizing Heavy Equipment Productivity
Here are some tips for optimizing heavy equipment productivity that can be applied to various projects-be it in the construction, mining, forestry, or agriculture sectors:
1. Choose the Right Tool as Needed
- Adjust the type and capacity of the machine to the type of work being done.
- Avoid using tools that are overcapacity or undercapacity because it will reduce work efficiency.
2. Train Operators Periodically
- Improve operator skills through regular training.
- Trained operators can operate tools more quickly, safely and fuel-efficiently.
3. Perform Periodic Maintenance and Inspection
- Schedule preventive maintenance to prevent sudden breakdowns.
- Ensure tools are always in ready-to-use condition and safe to use.
4. Use Monitoring and Telematics Systems
- Install GPS, fuel sensors and productivity monitoring tools to monitor performance in real-time.
- Analyze operational data to make fact-based decisions.
5. Optimize Heavy Equipment Work Cycle
- Reduce equipment idle time by speeding up the work cycle (loading, hauling, dumping, returning).
- Organize an efficient operational path with minimal disruption.
6. Pay Attention to Field and Weather Conditions
- Make repairs or level the terrain if it is too steep or muddy.
- Avoid operating in extreme weather which can degrade tool performance.
7. Create an Efficient Work Schedule
- Adjust work time to daily targets and tool capabilities.
- Avoid accumulation of tools or labor at one point.
8. Synchronize the Number and Type of Heavy Equipment
- Ensure that the ratio of equipment working together (such as excavators and dump trucks) is balanced.
- Avoid long waiting times between tools.
9. Improve Field Communication and Coordination
- Use a clear and consistent communication system between operators and supervisors.
- Good communication prevents operational errors and improves safety.
10. Periodic Productivity Evaluation
- Compare actual data with productivity targets.
- Conduct an evaluation to identify problems or areas of improvement.
You can also use the TransTRACK platform, which many of these tips can be automated through:
- Real-time monitoring of tools and operators
- Maintenance notifications
- Automatic productivity reports
- Efficiency and fuel consumption analysis
Machine productivity calculations are an important step in ensuring operational efficiency and overall project success. By understanding the factors that affect productivity and implementing the right optimization strategies, companies can reduce costs, accelerate project completion times, and improve team performance in the field.
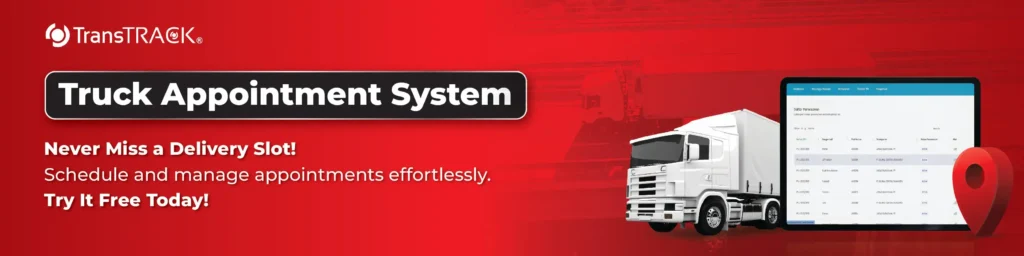
To support more integrated planning and management of heavy equipment, TransTRACK comes with a solution Truck Appointment System (TAS). This system allows you to automatically schedule the arrival and departure of vehicles, reduce waiting time, and improve coordination between machines and transport vehicles.
Optimize your machine’s productivity now with TransTRACK’s Truck Appointment System.
Contact us for a demo and more information.
Recent Post
Topic :