Optimize Supply Chain with Operational KPI Implementation!
Posted on August 29, 2024 by Nur Wachda Mihmidati
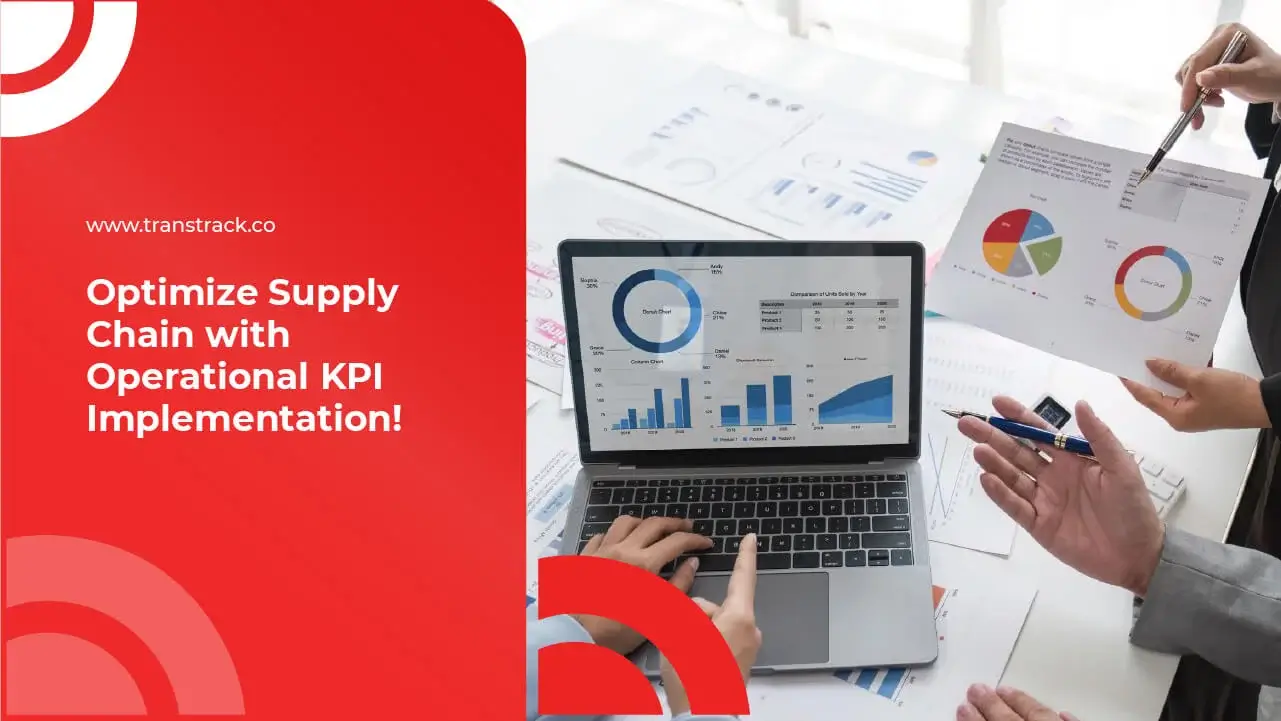
In an increasingly complex and competitive business world, companies are constantly looking for ways to improve their operational efficiency and performance. One way that has proven effective is by implementing KPIs (Key Performance Indicators) in supply chain management.
Based on the results of a study from Coyote, which involved nearly 1,000 shippers and 700 carriers across North America, it is clear that KPIs play an important role in a data-driven supply chain strategy. A total of 83% of shippers agree that KPIs are an essential part of a solid supply chain strategy, and 81% believe that their logistics KPIs are aligned with business strategy. Additionally, 75% of shippers feel they effectively communicate logistics KPIs to their internal teams, demonstrating the importance of a shared understanding among all team members to achieve efficient supply chain goals.
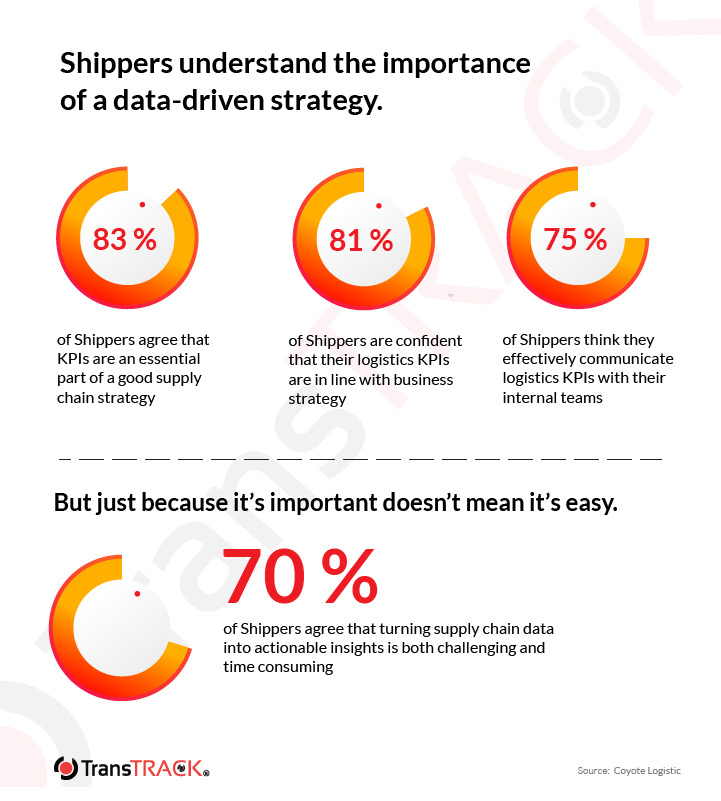
However, while many recognize the importance of KPIs and data-driven strategies, there are significant challenges in turning supply chain data into actionable insights. As many as 70% of submitters stated that this process is difficult and time-consuming. This demonstrates the urgent need for companies to improve their analytics capabilities and leverage data more effectively to optimize operations and achieve competitive advantage in the supply chain.
Key Challenges in Operational KPI Management
The main challenge in supply chain KPI management is data collection, management, and integration. This may be due to the fact that 56% of respondents still use manual and low-tech solutions such as spreadsheets to manage performance metrics. While there are technologies such as Enterprise Resource Planning (ERP), Transportation Management System (TMS), and Warehouse Management System (WMS) available, many businesses still rely on spreadsheets as their primary tool for managing KPIs.
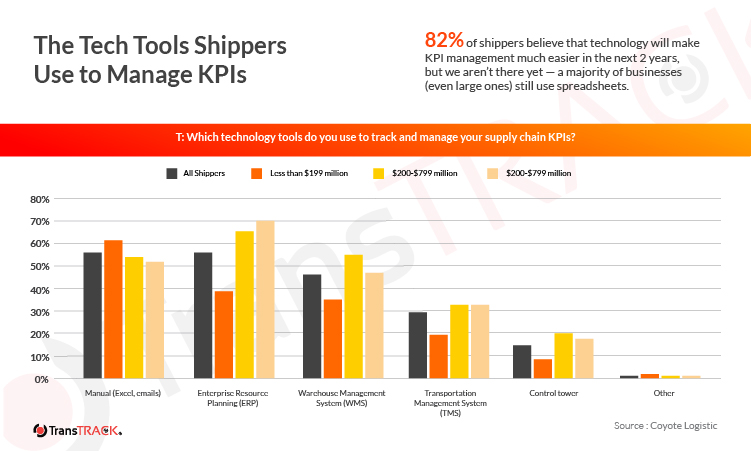
When viewed by business size, large companies more often use advanced technologies such as ERP (Enterprise Resource Planning) systems. About 70% of large companies and 66% of medium-sized companies use ERP to manage their KPIs, compared to only 39% in small companies. While many shippers want all their data integrated in one place, only 15% are currently using ‘control tower’ technology to integrate data, including only 19% of larger companies that have a larger budget for technology. Although 82% of shippers believe that technology will make managing KPIs easier in the next two years, many businesses still rely on a variety of different systems and tools. This requires a lot of manual work, so they need more manpower to manage and analyze the data.
Importance of Operational KPI in Supply Chain Efficiency
78% of shippers and 74% of carriers are in favor of industry standards being set for logistics KPIs. This shows the awareness and need for consistency in measuring operational performance across the sector. The agreement between the two groups emphasizes the importance of collaboration and standardization in achieving efficiency and reliability in the logistics supply chain. Standardizing KPIs can help improve communication, enhance service, and ensure that expectations are met consistently across the industry.
In the logistics industry, on-time delivery is the key performance metric (KPI) most favored by shippers. A total of 58% of shippers consider on-time delivery to be a very important KPI, with another 27% stating that it is moderately important. Other KPIs that shippers consider important include cost per shipment (47% very important), compliance with appointment scheduling (43% very important), and compliance with shipment tracking (41% very important). Other metrics such as cost per pallet and sustainability indicators also have significant levels of importance, but not as much as the focus on on-time delivery.
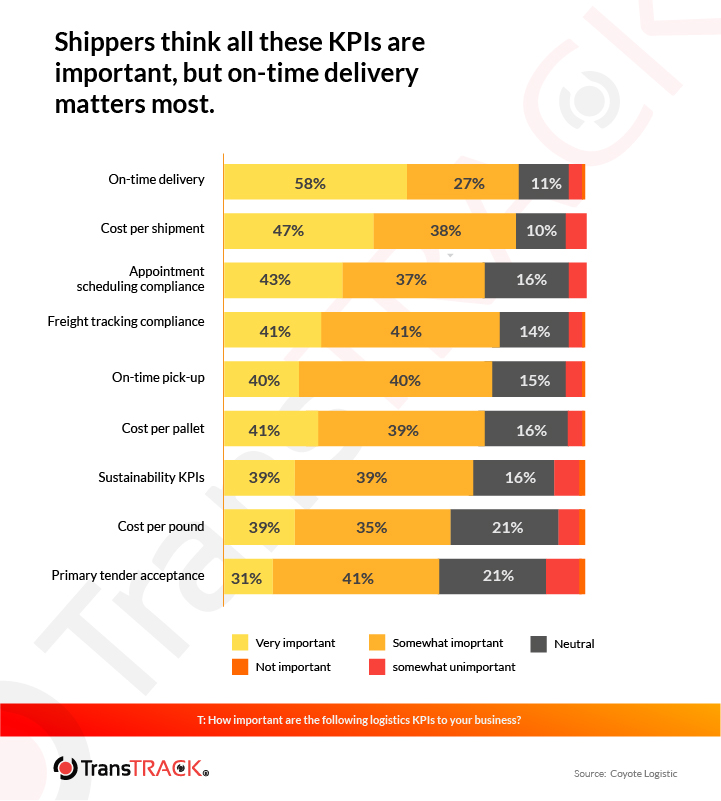
Industry Standard for Implementation of Operational KPI in Supply Chain
Based on the study, recommended industry standards for Key Performance Indicators (KPIs) in the supply chain. These KPIs are designed to assist shippers and carriers in achieving optimal and efficient performance.
Pick-up and Delivery Performance
Industry standards stipulate that pick-up and delivery performance should be 95% on-time. This means that goods should be picked up and delivered according to a predetermined schedule, with a maximum delay tolerance of 30 minutes. This percentage indicates the high level of reliability expected from logistics companies in maintaining customer satisfaction and operational efficiency.
Acceptance of Main Tenders
The acceptance rate of primary tenders is expected to reach 90%. This means that 90% of the tender offers submitted by customers or shippers should be accepted by the carrier. This figure reflects flexibility and responsiveness in meeting market demands and demonstrates the company’s ability to handle high volumes of work.
Payment Terms
Payment terms must be finalized within one week. This short payment time demonstrates the importance of smooth cash flow in supply chain operations, ensuring that all parties involved are compensated on time and can continue their operations without financial hindrance.
Cost/Revenue Measurement
Cost or revenue measurement is done per shipment. This allows companies to monitor and manage profitability in greater detail, as well as make strategic decisions based on the financial performance of each shipment transaction.
The implementation of this standard is expected to improve consistency and efficiency in logistics operations, strengthen trust between shippers and carriers, and support the overall growth and sustainability of the industry.
In facing the challenges of managing operational KPI, the implementation of modern management technologies such as Warehouse Management System (WMS) and Transportation Management System (TMS) is a very important solution. TransTRACK, as a platform that integrates WMS and TMS, offers the ability to monitor and manage KPIs in real-time, enabling shippers and carriers to achieve established industry standards, such as 95% on-time pickup and delivery performance, and 90% acceptance of major tenders.
With powerful analytics capabilities, TransTRACK facilitates more efficient data collection, management and integration. This reduces reliance on manual methods such as spreadsheets that are still used by 56% of respondents, thus helping to overcome the challenge of turning data into actionable insights. The technology enables companies to be more responsive to market demands, improve operational efficiency, and ensure high standards of compliance with logistics KPIs. In addition, TransTRACK’s ability to expedite payment processing within one week supports smooth cash flow, strengthens relationships with partners, and increases trust in the supply chain ecosystem.
By adopting TransTRACK, companies can achieve a competitive advantage through improved reliability, efficiency, and customer satisfaction, all of which contribute to long-term growth and sustainability in the logistics industry.
Recent Post
Find Out What Inbound Logistics is and How to Optimize It!
August 29, 2025Monitoring Fuel Expenditure Using Fuel Sensor
August 28, 2025Topic :