Cost Savings Through Operational Efficiency in the Mining Sector
Posted on October 1, 2024 by Nur Wachda Mihmidati
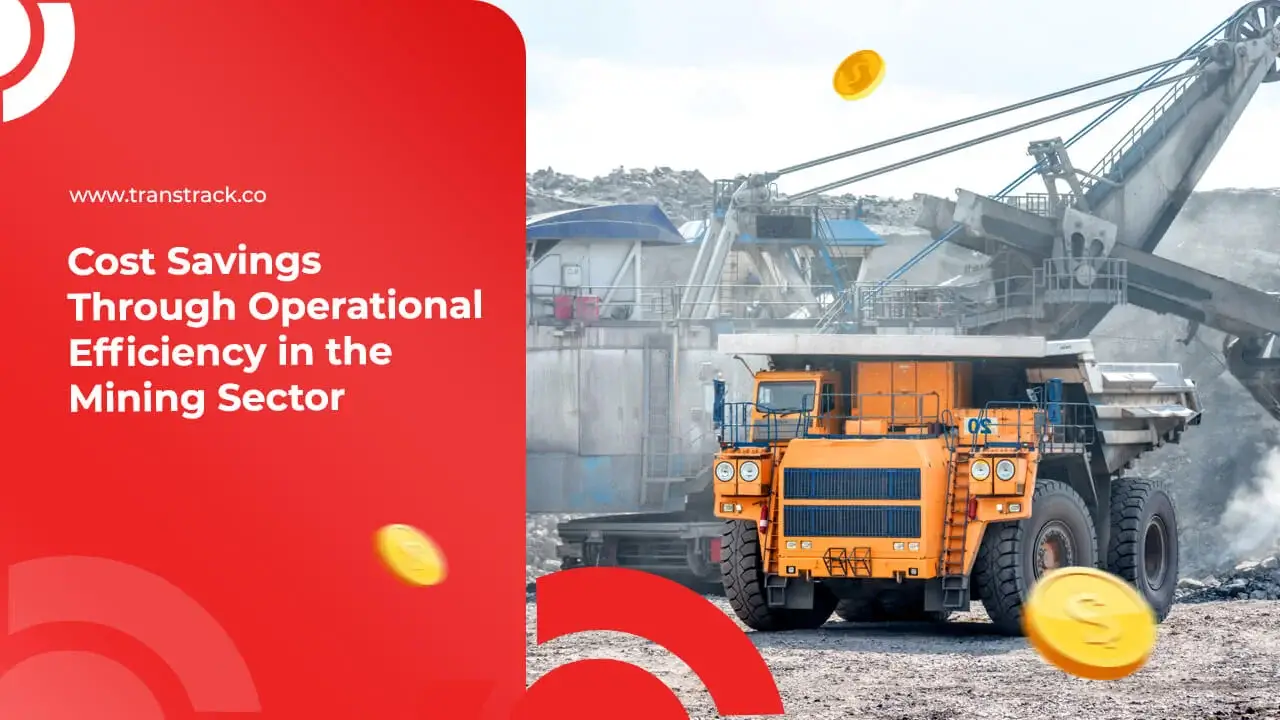
In the increasingly competitive world of mining, operational efficiency has become a critical success factor. With evolving challenges, such as rising costs and volatile demand, mining companies are required to adapt and find innovative ways to reduce expenses.
This TransTRACK article will review the strategic steps taken by several mining companies in improving their operational efficiency, as well as the significant impact they have made, both in terms of cost savings and increased productivity. Through case studies and analysis, we will see how the implementation of best practices and advanced technologies can open up new opportunities for companies to achieve sustainability and long-term growth.
Operational Efficiency Boosts Cost Savings at Mining Company
A mining company managed to significantly reduce operating costs after improving efficiency in various aspects of its operations. Steps taken included a review of the existing maintenance management system and the implementation of best practices for planning, scheduling and material management. The implementation of the new standardized maintenance management system resulted in lower man-hour requirements and improved productivity, resulting in a 14% reduction in labor costs.
In addition, the company reduced supplier contract costs by 9% through the review and negotiation of new contracts with key specialist suppliers. These business process improvements had a positive impact on the efficiency of material resource and inventory management, with stock values reduced by 12%. The overall result of this initiative was improved leaner operations and significant cost savings across all operational lines.
Improved Operational Efficiency Through Lean Production at East Mining Company
East Mining Company (EMCO), which operates on Sakhalin Island, Russia, managed to increase EBITDA by 14 million dollars in one year by implementing Lean Production principles. As a company that exports almost all of its coal output to the Asia-Pacific region, EMCO faced operational challenges caused by increasing production volumes and stripping ratios during the dynamic growth phase between 2016 and 2020. As the coal market stabilized, the company’s focus shifted from growth to operational efficiency. Through the implementation of Toyota Business Systems (TBS), EMCO successfully identified and eliminated operational inefficiencies resulting in increased production capacity and reduced costs.
One successful example is the optimization of dump truck filling using weight sensors to ensure maximum load without causing damage to equipment. In addition, EMCO incorporates processes such as refueling and lunch breaks to reduce downtime. The application of these Lean principles, including methods such as Total Productive Management (TPM) and standardization of operations, enabled EMCO to increase coal hauling volumes and significantly reduce equipment downtime. As a result, the company was able to increase productivity and substantially increase profit margins without the need for major investments in new equipment.
Productivity Improvement Through Digital Technology in the Mining Sector
The Australian mining industry is at a crossroads of significant opportunities and challenges. With lithium demand projected to increase 500-fold and copper demand expected to double, operational efficiency is key to meeting this demand. The implementation of digital technologies based on open standards could save up to US$370 billion in the mining sector by 2025 through reduced waste, increased productivity and improved safety. However, achieving this potential relies heavily on interoperability between the various systems and devices in the field.
At the Granny Smith mine, the implementation of a digital fleet management system integrated with the 4G network allows for fast and accurate transmission of data from deep underground to the control center. As a result, time lost due to communication errors is drastically reduced, resulting in a 30% increase in productivity in underground operations. In addition, the use of tablets for communication and work order delivery increases transparency and allows managers to make faster decisions. By reducing carbon emissions from motor vehicles that currently account for 40 to 50% of total mine site emissions, data-driven interoperability is becoming an important foundation for achieving sustainability in the mining industry.
TransTRACK Solutions in the Mining Industry
The mining industry faces various challenges, including improving operational efficiency, reducing emissions, and complying with safety regulations. TransTRACK’s solutions are the answer to improving productivity and sustainability in mining operations. By implementing advanced technologies such as digital fleet management systems and real-time monitoring, TransTRACK enables mining companies to optimize resource management and minimize downtime.
Below is an explanation of each feature of TransTRACK’s solutions for the mining industry:
Driver Monitoring System (DMS)
The Driver Monitoring System (DMS) is an innovative feature designed to improve safety in mining environments. By monitoring driver behavior in real-time, the DMS can detect signs of fatigue or distraction that could lead to an accident. This feature alerts drivers when danger signs are detected, allowing the company to take proactive steps to prevent incidents and ensure mine site safety.
Improved Operational Efficiency with Digital Fleet Management System
The Digital Fleet Management System offers comprehensive integration to manage all aspects of a mining fleet. By providing real-time information on vehicle location and status, it enables managers to make quick and informed decisions. Efficient fleet management not only improves productivity, but also optimizes resource usage and reduces overall operational costs.
Improved Operational Efficiency with Real-Time Monitoring
Internet of Things (IoT) technology enables real-time monitoring of equipment and resource conditions. This feature helps reduce downtime by alerting maintenance teams of urgent repair or maintenance needs. With access to real-time data, companies can identify issues before they become critical, thus maintaining smooth mine operations and maximizing efficiency.
Mobile Apps for Communication
The mobile application provided by TransTRACK facilitates efficient communication between workers in the field and managers in the control center. It reduces communication errors and improves team responsiveness by enabling instant information exchange. With better communication, projects can run more smoothly, reducing confusion and improving collaboration across the organization.
Data Analytics and Performance Reports
By providing in-depth analytical reports on operational performance and resource utilization, this feature assists management in strategic decision-making. The data generated provides important insights into trends and patterns that can be used to improve productivity. Proper analysis allows companies to identify areas that need improvement and optimize operational processes.
Open Platform and System Integration
The TransTRACK solution ensures interoperability between the various devices and systems used at the mine. By enabling seamless data exchange and collaboration between teams and systems, it eliminates information silos that often hamper operational efficiency. This allows companies to utilize all available technologies and increase overall productivity.
Carbon Emission Reduction
The TransTRACK system also focuses on reducing the carbon footprint by encouraging the use of electric vehicles and optimizing routes to reduce emissions. By monitoring emissions from fossil-fueled equipment, TransTRACK provides recommendations for improvements that can help companies achieve their sustainability targets. Reducing emissions is not only good for the environment, but can also improve a company’s reputation in the eyes of stakeholders.
User Training and Development
Comprehensive training is provided to ensure users can utilize all technology features effectively. By increasing worker engagement and expertise in operating the system, companies can achieve better results. This training also helps reduce resistance to technological change, enabling faster and more successful adoption in the work environment.
With innovative solutions from TransTRACK, the mining industry can improve operational efficiency and safety. Digital Fleet Management Systems and Driver Monitoring Systems (DMS) help optimize vehicle performance and reduce the risk of accidents. Contact the TransTRACK team today for a free consultation and improve productivity and sustainability at your mine site!
Recent Post
Find Out What Inbound Logistics is and How to Optimize It!
August 29, 2025Monitoring Fuel Expenditure Using Fuel Sensor
August 28, 2025Topic :