Latest Innovation in Fleet Management System for Plantation Sector
Posted on September 13, 2024 by Nur Wachda Mihmidati
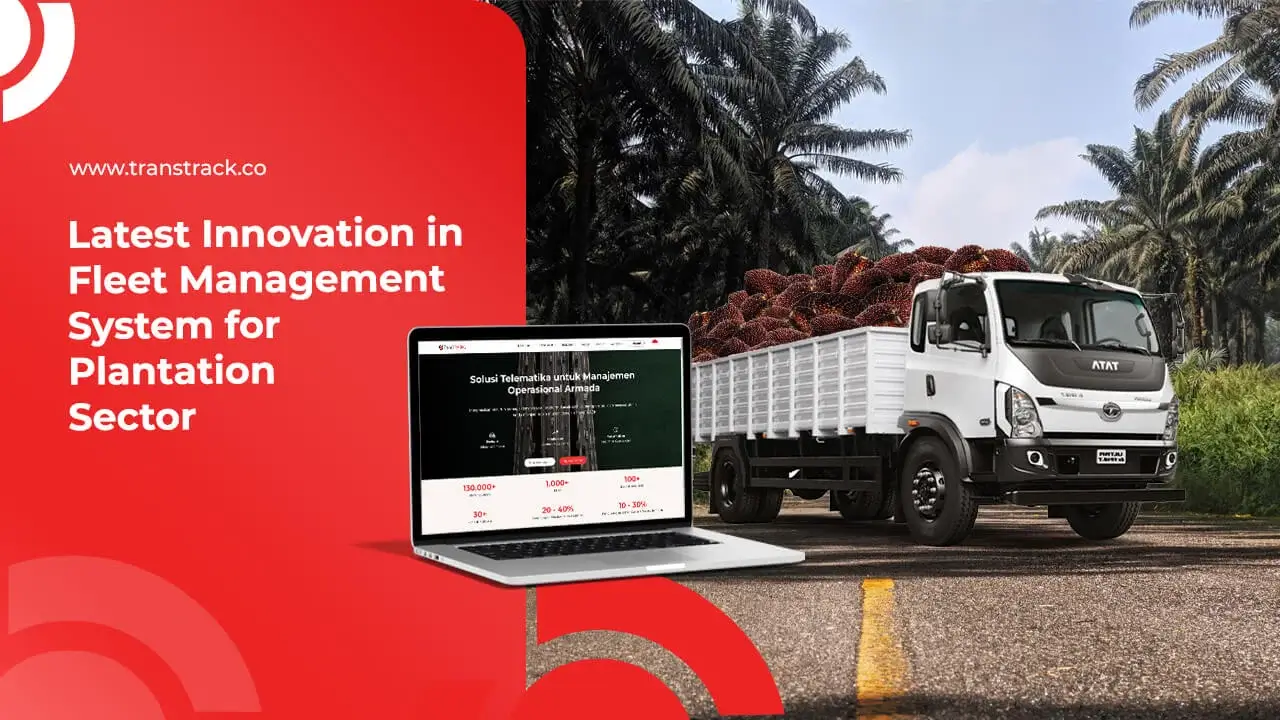
The harvesting process in the plantation industry, especially in commodity sectors such as palm oil and rubber, is a critical stage that not only determines production yields, but also contributes greatly to overall costs. Amidst demands to improve efficiency and profitability, cost analysis at the harvest stage has become very important. Various factors, ranging from labor costs to transportation, as well as the use of tools and equipment, play a significant role in shaping the cost structure that industry players must manage. Understanding this cost composition through fleet management system optimization can help plantation managers make strategic decisions to optimize available resources.
With diverse geographies and complex operational challenges, especially in remote areas, harvesting costs can be a significant burden. Therefore, an in-depth analysis of the factors that affect harvesting costs-such as the need for skilled labor, transportation of produce, and necessary tools-can open up opportunities to improve efficiency. This article aims to provide a comprehensive overview of the cost composition of the harvesting sector in the plantation industry, and identify strategies that can be implemented to reduce costs and improve overall productivity.
Cost Analysis in the Harvest Sector: Challenges in Labor and Transportation
In any agricultural production process, cost is an important factor that determines efficiency and profitability. One of the critical stages in the agricultural cycle is the harvesting process, where various cost components affect the overall operational cost. From labor, transportation, to the use of support equipment such as sickles, chisels, and push tools, all these elements contribute to the overall cost of harvesting.
In this context, analyzing the composition of harvesting costs is essential to identify the factors that affect the budget the most and how efficiency can be improved. The harvest cost distribution chart shown in this study provides an in-depth insight into how labor and transportation are the largest cost components, followed by equipment and other aids. A discussion of each section follows:
- Labor – 34% Labor is the largest cost component in the harvesting process at 34%. This shows that labor is an important factor that takes up a significant portion of the total cost, probably because harvesting requires a lot of manual or skilled labor.
- Transport – 26% Transportation ranks second with an allocation of 26%. This could include the cost of transporting the harvest from the field to storage or market. The size of this percentage could indicate difficult distances or terrain, or possibly high vehicle and fuel costs.
- Wheelbarrow – 17% Wheelbarrow costs account for 17%, indicating that they may be essential in moving large quantities of crops from one place to another. Its extensive use in this process affects the cost contribution.
- Aluminum rods – 7% The next component is aluminum rods with an allocation of 7%. These may be used for harvesting or preparing the produce, which in certain contexts is crucial for efficiency.
- Chisels – 7% Chisels also contribute 7% to the cost. Chisels are likely to be used in cutting or separating certain parts of the crop.
- Sharpening stones account for 5% of the total cost, which may be used to maintain the sharpness of harvesting tools such as sickles, which are essential for fast and efficient harvesting.
- Sickle – 2% The sickle accounts for only 2%, perhaps because the cost is low or the sickle is used on a smaller scale than other tools.
- Hook – 1% The hook is the component with the smallest percentage, only 1%. Perhaps this tool is used in specific situations or is only required in small quantities during the harvesting process.
From this data, it can be concluded that labor and transportation costs are the largest components in the harvesting process, while tools such as sickles, chisels, and aluminum sticks are also important despite having a smaller contribution to the overall cost. Efficiency in the use of tools and labor may be the key to further reducing production costs.
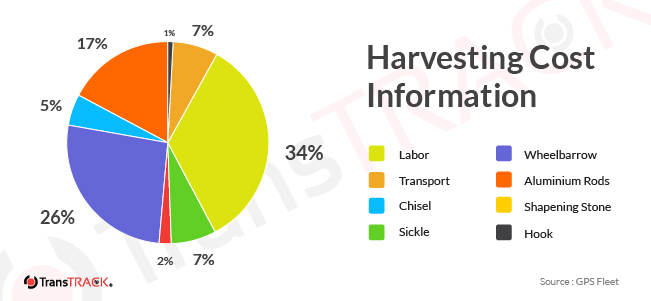
Optimization of Fleet Management System for Sustainable Palm Oil Production Efficiency
The acquisition of nearly 135,000 hectares of agricultural land by the world’s largest Sustainable Palm Oil producer, primarily in Papua New Guinea, presented significant operational challenges. With plantations located in remote and remote areas, operational cost and productivity analysis was difficult. To address these challenges, MTIS, as Banlaw’s Official Technology Partner, was brought in to implement a sophisticated process and technology solution to improve visibility into liquid resource management. The system implemented included strict access controls, enhanced data integration, and automated measurement and monitoring, allowing the company to more efficiently control fuel allocation and usage.
The impact of implementing the Banlaw system has been remarkable. In a short period of time, the company has achieved millions of dollars in fuel cost savings, with savings of approximately AUD 800,000 in the first year for the first upgraded site. In addition, with a 26% reduction in fuel consumption from January 2020 to January 2021, the company has been able to continue to improve its operational results. This automation process not only closes the gap between fuel paid for and received, but also enables further expansion at 12 additional locations, which in turn delivers substantial and sustainable savings.
TransTRACK Fleet Management System (FMS) Solution in Plantation Industry
TransTRACK offers a Fleet Management System (FMS) solution specifically designed to meet the needs of the plantation industry, such as palm oil, rubber, and other commodities. This solution facilitates the management of vehicle and machine fleets used in plantation operations, from transporting harvests to distributing them to storage or processing locations. With real-time monitoring features, TransTRACK allows plantation managers to get the latest information on the location, status, and performance of vehicles, so that decision-making can be done quickly and accurately.
The TransTRACK Fleet Management System also offers increased efficiency through route optimization and operational schedules. With careful data analysis, this system can identify the fastest and most efficient routes for delivery, reducing travel time, and saving fuel costs. In addition, the driver behavior analysis feature helps minimize accidents and improve work safety, which is very important in the plantation industry which often operates in remote and challenging areas. With the integration of advanced technologies such as sensors and mobile applications, TransTRACK provides a comprehensive solution to improve productivity and sustainability of operations in the plantation sector.
Let’s Join TransTRACK!
Want to improve the efficiency and productivity of your plantation operations? Contact us now for a free demo and discover how our Fleet Management System solution can change the way you manage your fleet and improve your yield!
Recent Post
Topic :