Case Study of Inventory Management Strategy to Face Market Challenges
Posted on September 18, 2024 by Nur Wachda Mihmidati
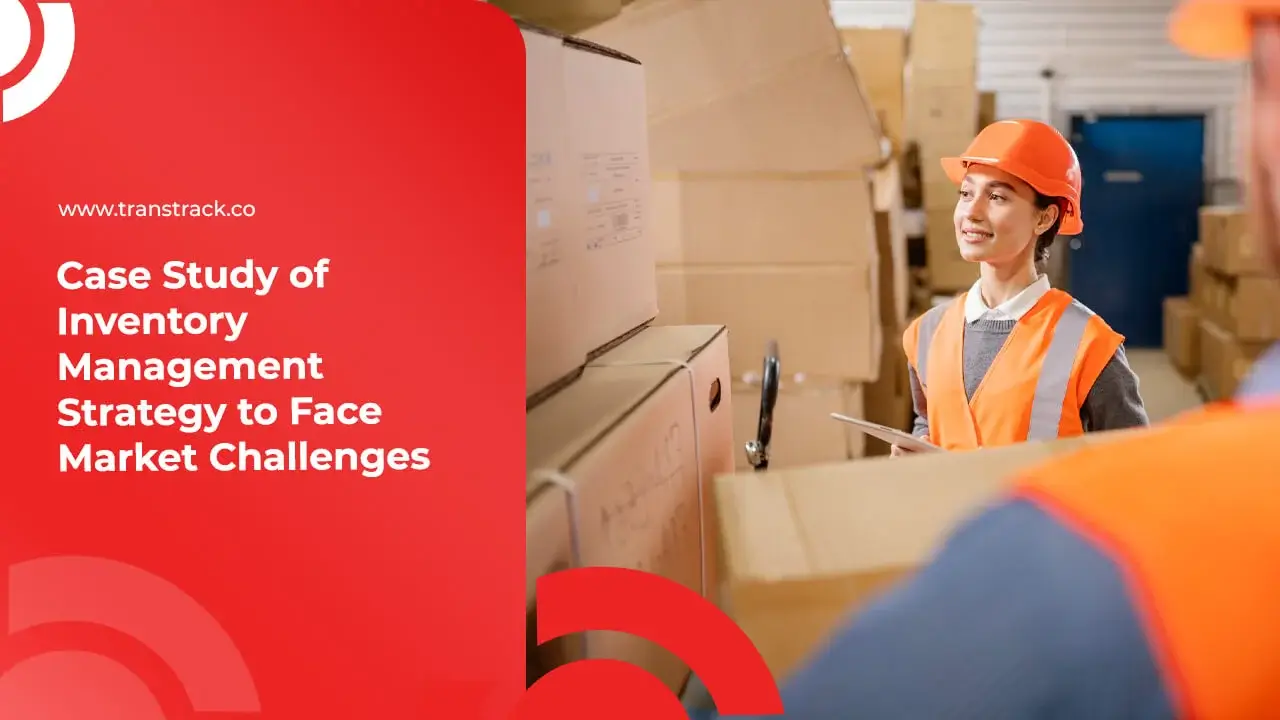
In an increasingly competitive business world, efficient inventory management is key to achieving operational success. In the logistics sector, particularly in warehouse management, the challenges companies face are increasingly complex, especially with increasing demand and market uncertainty. This is where it is important to adopt an advanced warehouse management system, such as TransTRACK’s Warehouse Management System (WMS). This system is designed to provide innovative solutions that not only improve operational efficiency, but also assist companies in responding to changes in demand quickly and accurately. In this article, we will explore the various features and advantages of WMS TransTRACK, as well as how this system can change the way companies manage their inventory and supply chain.
Inventory Management Optimization Overcomes Stock and Damage Challenges
In supply chain distribution, high inventory levels are often caused by a mismatch between sales and shipment forecasts and actual sales. The absence of a periodic process to review and update annual forecasts based on market feedback exacerbates this problem. A distribution system that drives supply without considering market needs is also a major factor. In addition, security stocks maintained in warehouses often far exceed agreed targets, with no effective monitoring system in place. Stock allotment was also done manually, which slowed down the process and increased the risk of errors.
Inventory of old, damaged or unsold items also increased as there was no clear visibility of inventory details across stock points. Monitoring of dead stock is not done effectively, and recording of slow-moving or damaged stock is not done accurately. Communication regarding dead stock is done manually, which is time-consuming and prone to errors. In addition, the inaccuracy of inventory recording was compounded by the absence of a clear policy regarding periodic reconciliation between physical stock and book records.
To address these issues, several process improvements were implemented. A bin card system was implemented for each shelf in the distribution center, with training to staff on record keeping. Periodic reconciliation of physical stock and book records was also required. IT solutions were implemented to automate security stock calculation, stock data communication, and stock allocation based on the FIFO (First-In, First-Out) principle. Demand planning and forecasting processes were also updated to be more dynamic and in line with market conditions. Strict measures were put in place to deal with damaged stock and dead stock, with clear responsibilities.
The results of these measures were significant. Within two months, inventory recording accuracy reached 95%, with a reduction in stock levels from 8.2 weeks to 5.5 weeks in the distribution center, and from 6.5 weeks to 4 weeks in the warehouse, including damaged stock. Transparency regarding saleable and damaged stock improved, enabling more accurate demand planning and stock allocation. Damaged stock handling is also improved, with sales of salvaged damaged stock at discounted prices and timely destruction of unusable products. In addition, the proportion of old and damaged stock is reduced, thus ensuring fresher products in the market.
The main causes of excess inventory include internal organizational practices, lack of strategic ownership, and ineffective policies in inventory management. While there are general studies on excess inventory management, industry-specific approaches are limited. The elevator industry, for example, has varied types of parts with different life cycles, which affects how its inventory is managed.
Effective Strategies to Reduce Excess Inventory in the Elevator Industry
The main causes of excess inventory in the elevator industry include data errors in planning parameters, inappropriate demand forecasting methods, lack of parts lifecycle management, and the existence of functional silos in the organization that favor the performance of certain teams. To reduce excess inventory, this paper suggests strategic approaches such as the implementation of large-volume purchasing policies, reverse logistics policies, and customer returns. In addition, the use of big data and business analytics is considered essential to minimize excess and dead stock.
Suggested proactive strategies include the application of appropriate demand forecasting techniques, such as the Croston/SBA method for infrequently needed items, as well as the utilization of risk profiling for parts that are nearing the end of their life cycle. The recommended reactive strategies involved lateral transshipment models, discounted sales, and scrapping of parts that were no longer in use. This approach proved successful in reducing excess inventory worth more than €3 million in three years.
Excess inventory management should be a strategic focus in inventory planning or supply chain optimization. The implementation of specialized algorithms and effective policies can help to significantly reduce excess inventory, particularly in the elevator industry.
In conclusion, effective inventory management is essential to meet the challenges of supply uncertainty. By implementing data-driven management strategies, companies can optimize storage processes, reduce demand uncertainty, and improve operational efficiency. Here, TransTRACK’s Warehouse Management System (WMS) comes as a superior solution to help companies face these challenges.
TransTRACK’s Warehouse Management System (WMS) is designed to improve operational efficiency and effectiveness within the warehouse. Here are some of its key advantages:
- Warehouse Process Automation: TransTRACK’s WMS automates various processes, from receiving goods to shipping. This reduces the possibility of human error and increases the speed of operations.
- Real-time Inventory Tracking: With real-time monitoring technology, users can accurately track the location and status of inventory, reducing the risk of stock-outs and excess inventory.
- Warehouse Setup Optimization: The system offers solutions for better organization of warehouse space, including strategic placement of goods based on sales frequency and product type. This improves picking and storage efficiency.
- Data Integration: TransTRACK WMS can be integrated with other systems in the supply chain, providing better visibility and data for managers to make better and faster decisions.
- Performance Analytics: With advanced analytics features, the system provides deep insights into operational performance, helping managers to identify areas for improvement and optimize processes.
- Improved Customer Service: With a more efficient system, companies can provide better services to customers, such as faster delivery and higher accuracy in order processing.
With TransTRACK’s WMS, companies can not only improve their operational efficiency, but also reduce costs and increase customer satisfaction. Invest in our system to transform your warehouse management to be more effective and responsive to market demands. Contact us for a demo or more information!
Recent Post
Topic :