Unraveling the Causes of the Bullwhip Effect and How to Overcome It
Posted on August 2, 2023 by Nur Wachda Mihmidati
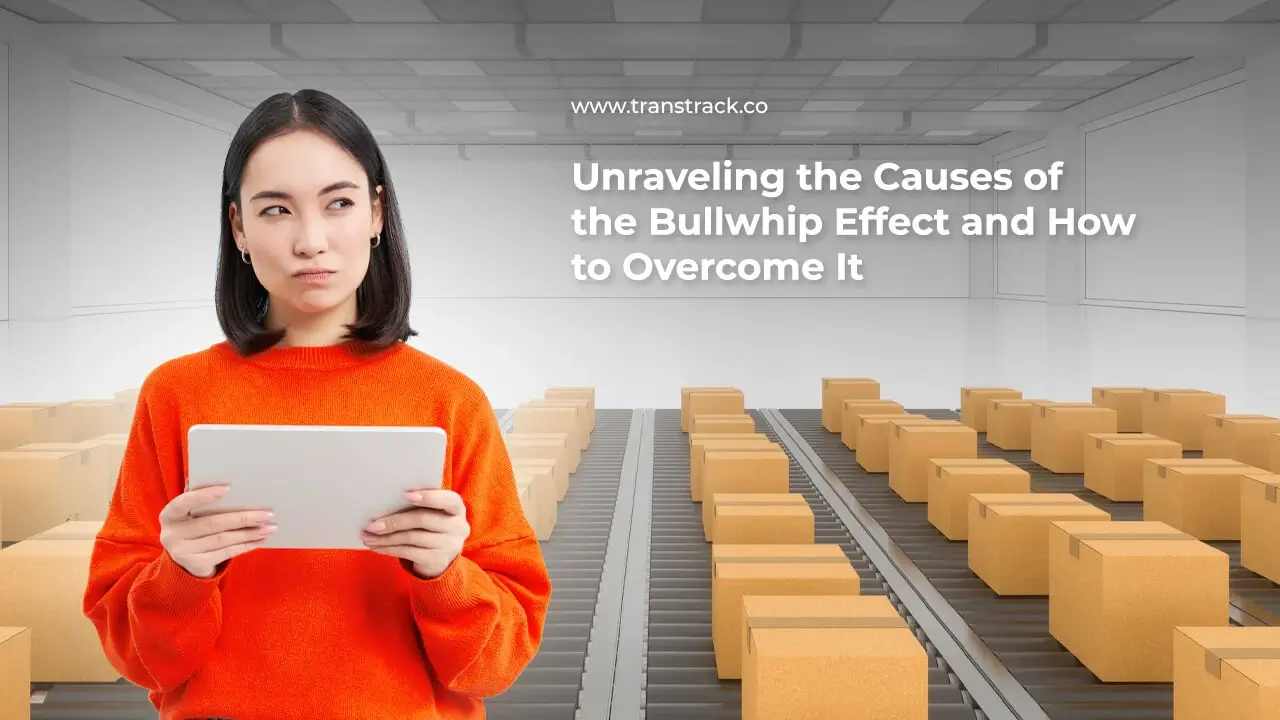
The bullwhip effect refers to the phenomenon where demand fluctuations in a supply chain exponentially amplify as they move from end consumers to producers. In a multi-stage supply chain, each stage tends to make demand forecasts based on limited information received from the previous stage.
In the bullwhip effect, small changes in demand at the end of the supply chain can result in significant demand changes at earlier stages. For example, if retailers observe a slight increase in demand from their customers, they may order more goods from distributors to anticipate the growth in demand. The distributors then pass on this change by ordering more raw materials or finished products from their suppliers. This effect continues at each stage of the supply chain, magnifying demand fluctuations and causing significant disruptions in inventory and production.
Causes of the Bullwhip Effect in the Supply Chain
Several factors contribute to the bullwhip effect, including:
Lead Time Issues
Lead time is the duration from the order placement to receipt of goods. Any delays in the shipping or production process can hinder the availability of accurate demand information. When customers experience delivery delays, they may order more goods to anticipate uncertainties and meet future needs. This leads to excessive demand at earlier stages of the supply chain, thereby amplifying the bullwhip effect.
Excessive Discounting and Promotions
Aggressive discounting and promotions can drastically affect demand patterns. When customers become aware of discounts or promotions, they tend to increase their order quantities. This results in disproportionate demand changes at each stage of the supply chain. Manufacturers and distributors then have to respond by ordering more goods to meet the “perceived” increased demand, without accurate information about the actual demand.
Erroneous Demand Forecasting
Inaccurate demand forecasting can be a primary cause of the bullwhip effect. If each stage in the supply chain uses inadequate forecasting methods, errors and mismatches in demand estimation accumulate as they move from end consumers to producers. These discrepancies lead to excessive or insufficient orders at each stage of the supply chain, magnifying demand fluctuations.
Manufacturing Costs
The bullwhip effect can increase production costs because fluctuating demand leads to changes in raw material requirements and production capacity. Inconsistent production can result in inefficient resource utilization and high overhead costs.
Inventory Costs
Disproportional demand fluctuations can cause excessive inventory buildup at various stages of the supply chain. This leads to higher inventory costs, including storage expenses, product obsolescence risks, and increased capital requirements.
Lead Time
The bullwhip effect can prolong delivery times and overall lead time. Fluctuating demand influences production and delivery decisions, which can result in delays in delivering goods to end customers.
Transportation Costs
Excessive demand changes can lead to imbalances in shipping volumes. This can result in inefficient transportation, such as partially empty shipments or emergency deliveries to meet sudden increases in demand.
Labor Costs for Shipping and Receiving
Unforeseen demand fluctuations can increase the workload for shipping and receiving activities. In high-demand situations, companies may need to hire additional labor or increase working hours to meet the demand. This contributes to increased labor costs.
Level of Product Availability
The bullwhip effect can cause an imbalance between demand and inventory levels. Sharp demand fluctuations at a particular stage can lead to shortages in subsequent stages, while previous stages may have excess inventory. This can disrupt product availability and reduce the level of customer service.
Relationship across the Supply Chain
The bullwhip effect can affect the relationships among supply chain partners. Mismatch between actual demand and inaccurate forecasts can result in mistrust and disappointment among business partners. This can impact collaboration and cooperation within the supply chain, leading to conflicts and difficulties in inventory planning and control.
Overall, the bullwhip effect has negative impacts on the supply chain, including increased production and inventory costs, longer lead times and transportation costs, increased labor costs, decreased product availability, and disruptions in inter-member relationships within the supply chain. To address the bullwhip effect, it is important to enhance coordination, collaboration, and accurate information exchange among supply chain members, as well as implement improved forecasting methods and efficient inventory management practices.
[display-post-read-also]
Ways to Address the Bullwhip Effect
Here are some approaches that can help overcome the bullwhip effect in the supply chain:
Simplify the Supply Chain
One way to reduce the bullwhip effect is by simplifying the supply chain. This can be achieved by reducing the number of stages involved in the supply chain or by shortening the lead time between each stage. By reducing complexity, information about demand can flow more quickly and accurately throughout the supply chain, minimizing unnecessary demand fluctuations.
Limit Promotions and Product Sales
Offering discounts, promotions, and special sales can trigger disproportionate increases in demand. To alleviate the bullwhip effect, companies can limit the frequency and scale of promotions to align them better with actual demand. Additionally, it is crucial to establish good coordination between marketing departments and the supply chain to utilize realistic demand estimates in inventory planning.
Optimize Minimum Order Quantity (MOQ)
Minimum Order Quantity (MOQ) refers to the minimum quantity that must be ordered for each shipment. In an effort to reduce the bullwhip effect, companies can optimize the MOQ to align with actual needs and stable demand. By reducing high MOQs, companies can avoid excessive inventory accumulation in various stages of the supply chain, thus minimizing excessive demand fluctuations.
Utilize Warehouse Management System Software
Employing advanced Warehouse Management System (WMS) software can help address the bullwhip effect. Such systems assist in real-time inventory monitoring, expedite order processing, and enhance delivery efficiency. By harnessing information technology, companies can improve inventory visibility throughout the supply chain, expedite information flow, and enhance demand forecasting accuracy.
In addition to the aforementioned measures, strong collaboration and coordination among supply chain members are crucial in tackling the bullwhip effect. By openly sharing information, utilizing accurate forecasting methods, and improving communication among business partners, the supply chain can become more responsive and efficient, reducing excessive demand fluctuations and optimizing overall supply chain performance.
In dealing with the bullwhip effect, which can disrupt supply chain performance, the use of TransTRACK’s Fleet Management System (FMS) can provide an effective solution. FMS is a fleet management system that helps improve operational efficiency, reduce transportation costs, and optimize cargo delivery.
Overall, the utilization of the Fleet Management System form TransTRACK can aid in addressing the bullwhip effect by enhancing visibility, efficiency, and accuracy in transportation and cargo management. By optimizing fleet operations and inventory planning, companies can reduce disproportionate demand fluctuations, enhance customer service, and achieve better supply chain performance.
Recent Post
Topic :